Did you know that 95% of new electronic products never make it past the prototype stage? Even those that reach the market often struggle due to design flaws, manufacturing issues, or poor market fit. Why Most Electronic Products Fail isn’t just about bad luck—it’s a result of avoidable mistakes. From rushed prototyping to overlooked compliance requirements, companies repeatedly fall into the same traps. In this blog, we’ll uncover common reasons for electronic product failure, explore real-world electronic product development mistakes, and share expert tips to ensure your next innovation doesn’t end up in the junk pile.
Common Reasons Why Electronic Products Fail:
Understanding why most electronic products fail can help businesses avoid costly mistakes. Below are the key factors that contribute to failure and how to overcome them:
Poor Market Research & Lack of Customer Demand:
One of the biggest common reasons for electronic product failure is poor market research. Many companies invest heavily in development without validating whether there’s actual demand for their product. Without proper research, businesses risk creating products that either solve non-existent problems or fail to differentiate from competitors. To prevent this, companies should conduct surveys, analyze competitors, and test prototypes with real users before mass production. Following best practices in electronic product development, such as launching a Minimum Viable Product (MVP), can save time and resources.
Design and Engineering Flaws:
Flawed design choices often lead to performance issues, overheating, or outright failure. One of the most common electronic product development mistakes is ignoring key engineering principles, such as proper PCB layout, power management, and thermal control. Additionally, using low-quality components can result in premature breakdowns. Avoiding pitfalls in electronics design requires rigorous prototyping, stress testing, and iterative improvements. Prioritizing durability, efficiency, and user experience in the design phase is essential for success.
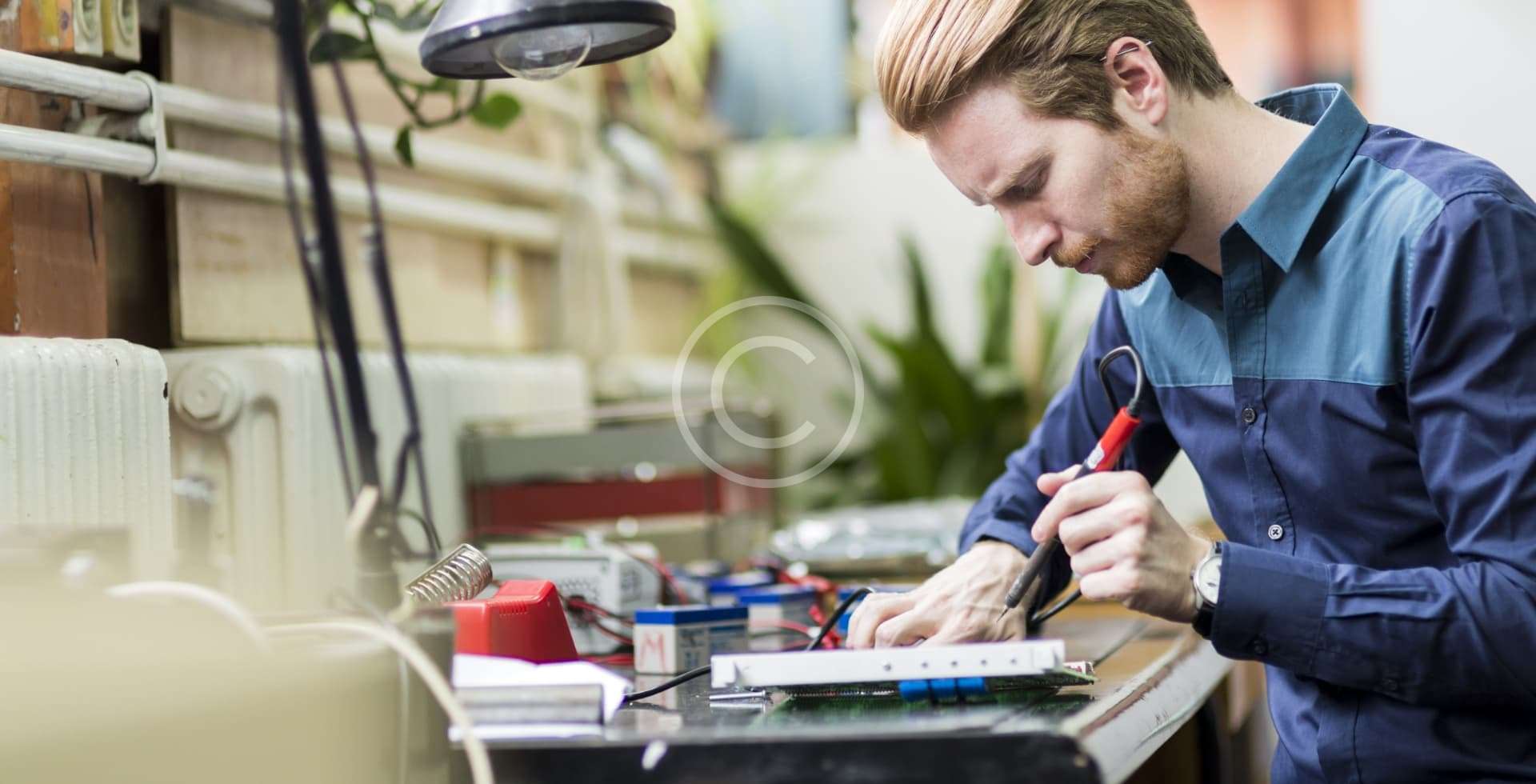
Manufacturing and Supply Chain Issues:
A great design won’t matter if production is plagued by delays, inconsistent quality, or excessive costs. Supply chain disruptions, unreliable suppliers, and poor material selection can lead to production failures. Many companies underestimate these challenges, leading to increased expenses and missed deadlines. Improving electronic product reliability starts with selecting reputable manufacturers, ensuring quality control at every stage, and having contingency plans for sourcing critical components.
Regulatory and Compliance Failures:
Skipping compliance testing can be a costly mistake. Regulatory standards (FCC, CE, UL, etc.) exist to ensure product safety and functionality, but many companies overlook them until it’s too late. This leads to failed certifications, recalls, and legal issues. A key reason why most electronic products fail is ignoring compliance requirements in early development stages. Companies should integrate compliance testing from the start, work with regulatory experts, and conduct pre-certification testing to avoid setbacks.
Underestimating Firmware & Software Development:
Hardware is only half of the equation—firmware and software play a crucial role in device functionality. A poorly optimized firmware can lead to security vulnerabilities, slow performance, or compatibility issues. Many electronic products fail due to buggy firmware that wasn’t thoroughly tested. Improving electronic product reliability involves seamless integration between hardware and software, regular updates, and security patches. Ensuring firmware is robust and efficient is one of the best practices in electronic product development that guarantees long-term success.
How to Avoid These Mistakes and Build a Successful Product?
To increase the chances of success, companies must take a proactive approach at every stage of development. Below are key strategies to prevent electronic product development mistakes and create high-quality, market-ready products.
Conduct Thorough Market Validation:
Before investing in development, businesses must confirm that their product solves a real problem and has a market fit. Many startups overlook this step, which is one of the common reasons for electronic product failure. Conducting surveys, analyzing competitors, and engaging with potential customers can provide crucial insights. Creating a Minimum Viable Product (MVP) and testing it with real users before full-scale production helps validate demand and refine the product concept.
Focus on Robust Product Design:
One major reason why most electronic products fail is poor design. Insufficient power management, improper PCB layouts, and overheating issues can lead to product malfunctions. Companies should prioritize avoiding pitfalls in electronics design by following best engineering practices, using high-quality components, and conducting extensive stress testing. Prototyping and iterative design improvements help catch and resolve issues early, reducing costly redesigns later.
Optimize Manufacturing & Supply Chain Strategy:
Many products fail due to supply chain disruptions, poor-quality components, or unexpected manufacturing issues. Companies should build strong relationships with reliable suppliers, maintain backup sourcing strategies, and implement strict quality control measures. Working closely with manufacturers during the early design phase ensures production feasibility and cost-effectiveness. Optimizing logistics and inventory management also prevents costly delays and stock shortages.
Ensure Compliance and Testing:
Ignoring compliance requirements can lead to legal challenges, product recalls, or market rejections. Companies should integrate regulatory compliance checks (FCC, CE, UL, etc.) from the early stages of development. Pre-certification testing helps identify issues before the final approval process. Conducting environmental, safety, and performance testing ensures that the product meets industry standards and avoids costly failures post-launch.
Prioritize Firmware and Software Development:
A well-designed electronic product is ineffective without stable firmware and software. Poorly optimized firmware can cause crashes, slow performance, or security vulnerabilities. To prevent electronic product development mistakes, teams must focus on seamless hardware-software integration, regular updates, and rigorous debugging. Cybersecurity should also be a priority, ensuring the product remains protected from potential threats.
Conclusion:
Avoiding failure in electronic product development requires careful planning, rigorous testing, and a deep understanding of market needs. By addressing common pitfalls—such as poor design, supply chain issues, and software flaws—companies can improve reliability and bring successful products to market. Following best practices in electronic product development, from thorough market validation to compliance testing, ensures a smoother path to launch. In a competitive industry, success isn’t just about innovation—it’s about execution. Take the right steps, and your product won’t end up as another statistic of failure.
FAQS
Poor market research and lack of demand often lead to product failures, as companies invest in products without validating customer needs.
Start by researching relevant certifications (FCC, CE, UL) early in development and conducting thorough testing to meet industry standards.
Optimize PCB design, choose cost-effective components, and build relationships with reliable suppliers to balance cost and quality.
Firmware plays a crucial role in device functionality, security, and performance. A well-optimized firmware ensures a smooth user experience and minimizes product failures.