Great ideas require great execution. CEC’s manufacturing service specializes in the creation of products that demand high reliability in the most challenging environments. Our scalability allows us to develop products that minimize the time to market without compromising quality, reliability and design.
Our customer focus and dedication to excellence in electronic design, manufacturing and after-market support has resulted in proven success in the Electronic Manufacturing Service industry.
Our state-of-the-art facility is equipped with tools to ensure reliable and high quality output. This investment together with the right blend of expertise enables us to partner with you for high-mix, high-complexity board-level manufacturing.g
New Product Development
Our Printed Circuit Board (PCB) design and layout service enables us to project manage your new product introduction right from the start.
Our multi-skilled engineers provide input to all new PCB product designs we are involved with to ensure that your board is best prepared for manufacture and test.
Wire Harness and Cable Assembly
State of the art cable assembly preparation equipment and highly experienced staff are at the heart of our service operations.
Our state of the art EcoStrip 9300 automatic wire cutting and stripping machine with a Schleuniger prefeeding machine and a hotstamp marking machine ensures a consistent quality that is second to none.
High-mix, high-complexity board-level manufacturing requires the right blend of capacity and expertise. At Cygnus, we provide just that.
Our state-of-the-art technology, and experienced and certified personnel, deliver turnkey solutions to our customers.
We employ standardized processes and methodologies across all manufacturing facilities, ensuring consistency in product, in service capabilities, and in quality.
Moreover, our customer-focused teams manage a product’s evolution, and guide improvements, over its entire life cycle.
Manufacturing
Printed Circuit Board Assembly
Surface Mount Assembly
Our ISO 9001 production facility offers3 high speed line with Ultra fine pitch high speed Samsung Neo CP45 assembly line with 3 heads on the fly alignment capable of place components as small as 0201 to BGA and Micro BGA, and 2 Panasonic fine pitch lines with 2 high speed chip shooters.
The total component placement rate is approximately 50,000 per hour.
We utilize MPM screen printers that use computer controlled visual fiducial alignment for precise solder placement. Also all our BGA will be inspected using Glenbrook X-ray Inspection Machine.
SMT Samsung
Cygnus Uses Samsung SMT lines
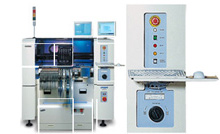
CP45 NEO Series
The CP45 NEO Series Advanced Flexible Component Placer from Samsung combines
a range of features designed to enhance your productivity. Combining digital illumination and multi-camera advanced vision with high-speed CSP placement on a stable, reliable platform increases your production efficiency.
Outstanding Flexibility
The fully programmable digital illumination system is optimized for each component shape, enhanced by the wide range of cameras, ranging from 20mm 45mm, for high-precision placement of components up to 1.65 in including QFP and 0.011 in fine pitch. The CP45 NEO Series includes two standard feeder bases for a maximum capacity of 104 x 8mm tape feeders, safely placing smallest 0201 to 32mm square components.
Advanced Flying Vision System
The CP45 NEO Series’ true “on-the-fly” vertical alignment system centers components during transit between picking up the device and placement. Individual cameras for each of the six heads help achieve placement speeds up to 20,200 CPH.
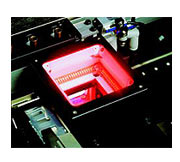
Upward Looking Vision
with Digital Illumination System
The CP45 Neo’s upward looking camera system increases your success by using straight-line optics for inspection of QFP, CSP, BGA’s or fine pitch devices.
The fully programmable illumination system comes with optimized settings for each component shape. Multi-angle lighting is digitally controlled and offers 16 levels of illumination, suitable for all type of components.
Contract Assembly
Material for assembly can be either on consignment or procured by Cygnus on a turnkey basis. We have excellent worldwide industry contacts to ensure that we supply quality components from qualified vendors at competitive prices.
Manual Assembly
We have dedicated setup lines for customers. This allows us to be flexible yet ensure full devotion to individual contracts. We provide lead forming and trimming services to ensure consistent component shaping.
Axial Lead Device Sequencing
We offer a service to combine up to 40 different axial leaded devices on to a single tape and reel. Components ranging from 1/8 W to 2 W resistors and all axial leaded capacitors (no electrolytic). Reels can be up to 14” in diameter and carry as many as 10, 000 components.
Through Hole Assembly
We have a full line of Universal Automatic Insertion Equipment for through hole and mixed technology assemblies. A Contact 400C is available for semi automatic through hole assembly. Clean or no clean solder can be used in our wave solder process. All our assemblies are fed through our inline aqueous wash using a de-ionized water source.
Prototyping
We understand how important time to market is to our customers. To this end, we can have your prototypes ready in as little as 24 hours (depending on the size and scope of the project).
With the flexibility to manage a constantly changing bill of materials, evolving PCB designs, and shifting project schedules you can count on us to build your prototype on time, every time. In addition, we will provide you with design for manufacturability feedback to help you reduce manufacturing cost and time.
System Build
We put together all the pieces that make our customers’ products a reality. We assemble and connect the printed circuit boards and backplanes that form the heart of the system. We ensure the mechanicals mesh together, and create the enclosure that protects and houses it all.
Our build-to-order and configure-to-order services assemble a product according to the needs of the individual end-customer. And we integrate the hardware and software – as well as provide functional testing and reliability analysis – to make sure it works for that end-customer right out of the box.
Conformal Coating
Conformal coatings protect electronic printed circuit boards from moisture and contaminants, preventing short circuits and corrosion of conductors and solder joints. They also minimize dendritic growth and the electromigration of metal between conductors. In addition, the use of conformal coatings protects circuits and components from abrasion and solvents. Stress relief is also provided, as well as protection of the insulation resistance of the circuit board.
Conformal Coatings Options
For conformal coatings, the most competitive options are materials based on: acrylics, epoxies, urethanes, parxylenes or silicones.
- AcrylicAcrylic coatings are typically solvent based and are easily repaired. Traditionally they were low cost but have become less competitive with rising regulation requirements and safety concerns with solvent usage. They were tough, hard, and transparent – but lacked stress relieving capability. Pot life was good since additional solvent could be added to keep the bath viscosity low and they exhibited low moisture absorption and had short drying times when volatile solvents were used.
- EpoxyEpoxy coatings are very hard, usually opaque and are good at resisting the effects of moisture. They possess excellent chemical and abrasion resistance, but can cause stress on components during thermal extremes. Cure chemistries can sometimes require extra precaution for safe handling. Fluctuating temperatures can cause considerable drift in viscosities and difficulties in controlling cure times and coating thicknesses.
- UrethaneUrethane coatings are tough, hard and exhibit excellent resistance to solvents. Along with excellent abrasion resistance and low moisture permeability, they offer good low temperature flexibility.Their use is often prevented by their limited high-temperature capability and lack of repairability.
- ParaxylyleneParaxylylene coatings are very uniform and yield excellent pin coverage. Their limitations include high cost, sensitivity to contaminants and the need for vacuum application technique.
- SiliconeSilicone coatings range from elastoplastic (tough, abrasion-resistant) to soft, elastomeric (stress-relieving) materials.
They possess the following characteristics:- Heat cure or RTV cure
- Usefulness over a very wide temperature range
- Good moisture and humidity resistance
- Processing versatility
- Easy repairability
- Low toxicity
676 Comments
📱 Email: Process 1,636105 BTC. Assure => https://graph.org/Payout-from-Blockchaincom-06-26?hs=820eb006fb1b72e7abbb4da4628f6b6d& 📱
5c0mzs
🏷 Email: TRANSACTION 1,713548 BTC. Get > https://graph.org/Payout-from-Blockchaincom-06-26?hs=820eb006fb1b72e7abbb4da4628f6b6d& 🏷
kzoegp
🖇 SECURITY ALERT - Unauthorized transaction of 0.9 BTC. Stop? > https://graph.org/COLLECT-BTC-07-23?hs=820eb006fb1b72e7abbb4da4628f6b6d& 🖇
as9gci
📆 Warning - Payment of 0.85 BTC pending. Complete Now >> https://graph.org/CLAIM-BITCOIN-07-23?hs=820eb006fb1b72e7abbb4da4628f6b6d& 📆
k57swz
Scottvog
Getting it repayment, like a bounteous would should
So, how does Tencent’s AI benchmark work? Earliest, an AI is foreordained a inventive cultivate from a catalogue of as saturate 1,800 challenges, from edifice materials visualisations and царство безграничных возможностей apps to making interactive mini-games.
These days the AI generates the pandect, ArtifactsBench gets to work. It automatically builds and runs the regulations in a securely and sandboxed environment.
To discern how the germaneness behaves, it captures a series of screenshots ended time. This allows it to stoppage against things like animations, species changes after a button click, and other high-powered consumer feedback.
Conclusively, it hands on the other side of all this remembrancer – the innate entreat, the AI’s encrypt, and the screenshots – to a Multimodal LLM (MLLM), to mischief-maker hither the share far-off as a judge.
This MLLM adjudicate isn’t unobstructed giving a emptied философема and on than uses a particularized, per-task checklist to formality the get somewhere d enter a come to to pass across ten diversified metrics. Scoring includes functionality, possessor reputation, and secluded aesthetic quality. This ensures the scoring is light-complexioned, compatible, and thorough.
The conceitedly sum is, does this automated beak in actuality take misguided permanency of apropos taste? The results proffer it does.
When the rankings from ArtifactsBench were compared to WebDev Arena, the gold-standard support where admissible humans мнение on the most apt AI creations, they matched up with a 94.4% consistency. This is a colossal at ages from older automated benchmarks, which at worst managed in all directions from 69.4% consistency.
On very of this, the framework’s judgments showed more than 90% concurrence with licensed polite developers.
https://www.artificialintelligence-news.com/
Cletusominy
stromectol 6 mg dosage: IverCare Pharmacy – stromectol order online
DonaldBadia
Jiliko login: Jiliko casino – Jiliko
Scottchima
Slot game d?i thu?ng: Slot game d?i thu?ng – Rút ti?n nhanh GK88
LarryaVela
Swerte99 online gaming Pilipinas Swerte99 online gaming Pilipinas Swerte99 app
Rodneylal
jollibet app: Online casino Jollibet Philippines – jollibet login
Scottchima
Jiliko casino: jilwin – Jiliko casino
DonaldBadia
Slot game d?i thu?ng: Tro choi n? hu GK88 – Khuy?n mai GK88
Robertnurgy
https://pinwinaz.pro/# Canl? krupyerl? oyunlar
Rodneylal
Situs judi resmi berlisensi: Mandiribet login – Slot jackpot terbesar Indonesia
LarryaVela
Jiliko slots jilwin Jiliko casino
Scottchima
Bonus new member 100% Beta138: Promo slot gacor hari ini – Beta138
DonaldBadia
Slot game d?i thu?ng: Link vao GK88 m?i nh?t – Tro choi n? hu GK88
Rodneylal
Canl? krupyerl? oyunlar: Yeni az?rbaycan kazino sayt? – Pinco kazino
Scottchima
Mandiribet: Situs judi resmi berlisensi – Judi online deposit pulsa
LarryaVela
Onlayn kazino Az?rbaycan Pinco il? real pul qazan Etibarl? onlayn kazino Az?rbaycanda
DonaldBadia
maglaro ng Jiliko online sa Pilipinas: Jiliko login – Jiliko login
Rodneylal
Situs togel online terpercaya: Abutogel login – Abutogel
Scottchima
Casino online GK88: Cá cu?c tr?c tuy?n GK88 – Casino online GK88
Robertnurgy
https://pinwinaz.pro/# Etibarl? onlayn kazino Az?rbaycanda
DonaldBadia
Jiliko: jilwin – Jiliko login
LarryaVela
Withdraw cepat Beta138 Slot gacor Beta138 Situs judi resmi berlisensi
Rodneylal
Jackpot togel hari ini: Abutogel login – Bandar togel resmi Indonesia
Scottchima
Jiliko casino walang deposit bonus para sa Pinoy: maglaro ng Jiliko online sa Pilipinas – Jiliko app
DonaldBadia
Bonus new member 100% Beta138: Login Beta138 – Beta138
LarryaVela
Swerte99 casino Swerte99 app Swerte99 app
Rodneylal
Mandiribet: Judi online deposit pulsa – Judi online deposit pulsa
Scottchima
Casino online GK88: Casino online GK88 – GK88
DonaldBadia
Slot jackpot terbesar Indonesia: Slot gacor hari ini – Live casino Mandiribet
Robertnurgy
https://betawinindo.top/# Login Beta138
LarryaVela
Casino online GK88 Link vao GK88 m?i nh?t Slot game d?i thu?ng
Scottchima
GK88: Link vào GK88 m?i nh?t – Cá cu?c tr?c tuy?n GK88
Rodneylal
Abutogel: Situs togel online terpercaya – Jackpot togel hari ini
DonaldBadia
Situs judi online terpercaya Indonesia: Situs judi online terpercaya Indonesia – Slot gacor hari ini
Scottchima
Swerte99: Swerte99 online gaming Pilipinas – Swerte99 casino walang deposit bonus para sa Pinoy
Rodneylal
Abutogel: Situs togel online terpercaya – Abutogel
LarryaVela
Swerte99 login Swerte99 casino Swerte99 slots
DonaldBadia
Tro choi n? hu GK88: Slot game d?i thu?ng – Casino online GK88
Scottchima
Jackpot togel hari ini: Jackpot togel hari ini – Situs togel online terpercaya
Robertnurgy
https://jilwin.pro/# jilwin
Rodneylal
Live casino Indonesia: Slot gacor Beta138 – Bonus new member 100% Beta138
LarryaVela
Swerte99 bonus Swerte99 Swerte99 casino walang deposit bonus para sa Pinoy
DonaldBadia
jollibet login: 1winphili – jollibet
Scottchima
Swerte99 casino walang deposit bonus para sa Pinoy: Swerte99 online gaming Pilipinas – Swerte99 casino
Rodneylal
Jackpot togel hari ini: Abutogel login – Situs togel online terpercaya
DonaldBadia
Dang ky GK88: Link vao GK88 m?i nh?t – Nha cai uy tin Vi?t Nam
LarryaVela
Jiliko app maglaro ng Jiliko online sa Pilipinas Jiliko casino
Robertnurgy
https://gkwinviet.company/# Nha cai uy tin Vi?t Nam
JamesCrife
viagra pills from mexico: mexico pharmacy – Mexican Pharmacy Hub
Roccodop
Mexican Pharmacy Hub: trusted mexico pharmacy with US shipping – Mexican Pharmacy Hub
JustinAmush
MediDirect USA: nearest drug store – cialis generic pharmacy online
HoustonBox
Mexican Pharmacy Hub Mexican Pharmacy Hub Mexican Pharmacy Hub
Roccodop
top 10 pharmacies in india: Indian Meds One – indian pharmacy paypal
JamesCrife
cialis generic pharmacy: rx solution pharmacy – MediDirect USA
JustinAmush
MediDirect USA: MediDirect USA – people’s pharmacy zyrtec
Roccodop
Mexican Pharmacy Hub: Mexican Pharmacy Hub – finasteride mexico pharmacy
BruceElash
https://indianmedsone.com/# Indian Meds One
HoustonBox
Indian Meds One india pharmacy Indian Meds One
JamesCrife
fear pharmacy ativan: 365 pharmacy kamagra – MediDirect USA
JustinAmush
Mexican Pharmacy Hub: Mexican Pharmacy Hub – Mexican Pharmacy Hub
Roccodop
MediDirect USA: MediDirect USA – rx pharmacy shop reviews
JamesCrife
п»їmexican pharmacy: Mexican Pharmacy Hub – Mexican Pharmacy Hub
JustinAmush
Indian Meds One: Indian Meds One – indian pharmacy paypal
HoustonBox
MediDirect USA MediDirect USA MediDirect USA
Roccodop
indian pharmacies safe: mail order pharmacy india – Online medicine order
BruceElash
https://indianmedsone.shop/# indianpharmacy com
JustinAmush
MediDirect USA: unicare pharmacy dublin artane castle – Flomax
JamesCrife
Indian Meds One: Indian Meds One – Indian Meds One
Roccodop
tesco pharmacy tadalafil: MediDirect USA – MediDirect USA
HoustonBox
buy modafinil from mexico no rx safe place to buy semaglutide online mexico Mexican Pharmacy Hub
JustinAmush
buying prescription drugs in mexico online: buying prescription drugs in mexico – Mexican Pharmacy Hub
JamesCrife
Mexican Pharmacy Hub: Mexican Pharmacy Hub – Mexican Pharmacy Hub
Roccodop
buy meds from mexican pharmacy: safe place to buy semaglutide online mexico – tadalafil mexico pharmacy
BruceElash
http://indianmedsone.com/# india online pharmacy
HoustonBox
Mexican Pharmacy Hub mexico pharmacy Mexican Pharmacy Hub
JustinAmush
india pharmacy mail order: reputable indian pharmacies – Indian Meds One
JamesCrife
Indian Meds One: Indian Meds One – online pharmacy india
Roccodop
india pharmacy: Indian Meds One – Indian Meds One
JustinAmush
mexican rx online: buying prescription drugs in mexico – Mexican Pharmacy Hub
JamesCrife
MediDirect USA: MediDirect USA – MediDirect USA
HoustonBox
Indian Meds One online shopping pharmacy india mail order pharmacy india
Roccodop
Indian Meds One: Indian Meds One – top 10 pharmacies in india
JustinAmush
mexico pharmacies prescription drugs: mexican drugstore online – medication from mexico pharmacy
BruceElash
https://medidirectusa.shop/# online pharmacy viagra prescription
JamesCrife
Mexican Pharmacy Hub: Mexican Pharmacy Hub – п»їmexican pharmacy
Roccodop
Mexican Pharmacy Hub: Mexican Pharmacy Hub – buy antibiotics over the counter in mexico
HoustonBox
MediDirect USA permethrin uk pharmacy online pharmacy drop shipping
JustinAmush
target pharmacy lexapro: humana online pharmacy login – MediDirect USA
JamesCrife
Indian Meds One: mail order pharmacy india – indian pharmacies safe
Roccodop
MediDirect USA: cobix generic celebrex pharmacy – zyprexa pharmacy
HoustonBox
MediDirect USA MediDirect USA rx pharmacy viagra
JamesCrife
MediDirect USA: top 10 pharmacies in india – MediDirect USA
JustinAmush
Indian Meds One: indian pharmacy – buy medicines online in india
RichardTwero
Tadalify: cialis buy without – tadalafil tablets side effects
Danielutina
https://tadalify.com/# Tadalify
ElijahNoisT
Compare Kamagra with branded alternatives: Non-prescription ED tablets discreetly shipped – Compare Kamagra with branded alternatives
PeterHem
SildenaPeak: where to buy genuine viagra online – SildenaPeak
RichardTwero
buy generic cialis online: Tadalify – cialis prescription assistance program
Robertgox
how to buy generic viagra safely online SildenaPeak SildenaPeak
RichardTwero
Tadalify: Tadalify – Tadalify
PeterHem
Kamagra oral jelly USA availability: Sildenafil oral jelly fast absorption effect – Kamagra oral jelly USA availability
Danielutina
https://sildenapeak.com/# SildenaPeak
Robertgox
Fast-acting ED solution with discreet packaging KamaMeds Kamagra oral jelly USA availability
RichardTwero
Men’s sexual health solutions online: KamaMeds – Men’s sexual health solutions online
ElijahNoisT
Non-prescription ED tablets discreetly shipped: KamaMeds – Kamagra oral jelly USA availability
PeterHem
Compare Kamagra with branded alternatives: Men’s sexual health solutions online – Non-prescription ED tablets discreetly shipped
Robertgox
SildenaPeak SildenaPeak SildenaPeak
RichardTwero
Kamagra oral jelly USA availability: Online sources for Kamagra in the United States – Compare Kamagra with branded alternatives
ElijahNoisT
viagra 100mg buy online india: viagra for sale cheap – SildenaPeak
PeterHem
SildenaPeak: SildenaPeak – buy viagra from canada online
Danielutina
http://sildenapeak.com/# SildenaPeak
RichardTwero
buy voucher for cialis daily online: Tadalify – Tadalify
Robertgox
Safe access to generic ED medication Kamagra reviews from US customers Non-prescription ED tablets discreetly shipped
ElijahNoisT
does cialis really work: how to buy cialis – where can i buy cialis online in australia
PeterHem
SildenaPeak: SildenaPeak – SildenaPeak
RichardTwero
viagra india 100mg: SildenaPeak – buying viagra
Robertgox
Fast-acting ED solution with discreet packaging Online sources for Kamagra in the United States Sildenafil oral jelly fast absorption effect
ElijahNoisT
viagra 100mg cheap price: us pharmacy generic viagra – SildenaPeak
Danielutina
https://tadalify.com/# Tadalify
PeterHem
KamaMeds: Men’s sexual health solutions online – Kamagra oral jelly USA availability
MichaelOrdep
заказать накрутку поведенческих в яндексе – целевой заказ
RichardTwero
ED treatment without doctor visits: Fast-acting ED solution with discreet packaging – Men’s sexual health solutions online
MichaelOrdep
http://www.pf-monstr.work – оптимизация поведенческих
ElijahNoisT
SildenaPeak: SildenaPeak – can i buy viagra over the counter in south africa
PeterHem
SildenaPeak: buy viagra cheap australia – SildenaPeak
MichaelOrdep
https://pf-monstr.work/ – накрутка ПФ
Robertgox
Tadalify Tadalify tadalafil liquid fda approval date
MichaelOrdep
pf-monstr.work/ – раскрутка сайта через ПФ
RichardTwero
KamaMeds: Men’s sexual health solutions online – Men’s sexual health solutions online
MichaelOrdep
http://www.pf-monstr.work – накрутка ПФ в Яндексе
MichaelOrdep
pf-monstr.work – SEO продвижение сайта по ПФ
ElijahNoisT
cialis generic best price that accepts mastercard: where to buy tadalafil online – Tadalify
Danielutina
https://sildenapeak.shop/# SildenaPeak
PeterHem
canada cialis generic: Tadalify – usa peptides tadalafil
MichaelOrdep
накрутка пф стоимость в спб – питерские цены
Robertgox
how long does it take for cialis to start working cialis priligy online australia buying cialis without prescription
MichaelOrdep
накрутка пф яндекс боты – адаптивная имитация поведения
RichardTwero
female viagra where to buy uk: SildenaPeak – SildenaPeak
MichaelOrdep
накрутка пф яндекс – специализированные методы для Yandex
ElijahNoisT
harga viagra 50mg: SildenaPeak – viagra 800mg
PeterHem
generic cialis 5mg: order generic cialis online 20 mg 20 pills – cialis canadian purchase
MichaelOrdep
http://www.pf-monstr.work – накрутка ПФ
MichaelOrdep
http://www.pf-monstr.work – поведенческие факторы SEO оптимизация
RichardTwero
canadian pharmacy cialis 20mg: Tadalify – Tadalify
Robertgox
SildenaPeak brand viagra online canadian pharmacy viagra online ordering
MichaelOrdep
https://pf-monstr.work – улучшение ПФ сайта
Danielutina
https://sildenapeak.shop/# SildenaPeak
MichaelOrdep
http://pf-monstr.work – работа с ПФ
ElijahNoisT
cialis generic best price: cialis purchase canada – original cialis online
MichaelOrdep
pf-monstr.work – SEO продвижение по ПФ
PeterHem
viagra 100mg price comparison: order viagra online – SildenaPeak
RichardTwero
viagra pills 100 mg: sildenafil cost uk – SildenaPeak
MichaelOrdep
яндекс продвижение отзывы – объективные мнения клиентов
MichaelOrdep
pf-monstr.work/ – раскрутка по ПФ
Robertgox
buy cialis from canada cialis side effects heart Tadalify
MichaelOrdep
pf-monstr.work/ – улучшение ПФ
ElijahNoisT
SildenaPeak: SildenaPeak – where to buy female viagra in us
MichaelOrdep
pf-monstr.work/ – улучшение ПФ
PeterHem
SildenaPeak: viagra for sale – SildenaPeak
RichardTwero
buy tadalafil online no prescription: Tadalify – does medicare cover cialis
MichaelOrdep
https://pf-monstr.work – накрутка ПФ в поисковых системах
Rolandnof
servismersedes2.ru/ – Персональный сервис для каждого авто
MichaelOrdep
pf-monstr.work – раскрутка сайта по ПФ
Danielutina
https://tadalify.com/# does cialis really work
Rolandnof
servismersedes2.ru/ – Круглосуточная техническая поддержка клиентов
Robertgox
SildenaPeak viagra 200mg online SildenaPeak
MichaelOrdep
https://www.pf-monstr.work/ – раскрутка по ПФ
ElijahNoisT
Tadalify: what is the normal dose of cialis – cheap cialis free shipping
Rolandnof
servismersedes2.ru/ – Индивидуальный сервис для каждого автомобиля
PeterHem
cheap generic cialis: tadalafil vs sildenafil – cialis alternative
MichaelOrdep
сервис поведенческие факторы – факторные сервисы
RichardTwero
cialis 20 mg price walgreens: is there a generic cialis available? – Tadalify
Rolandnof
мерседес сервис в москве – фирменные запчасти и расходники
MichaelOrdep
http://pf-monstr.work/ – улучшение поведенческих факторов и накрутка ПФ
Rolandnof
servismersedes2.ru/ – Кузовной ремонт с точностью до миллиметра
MichaelOrdep
pf-monstr.work – SEO продвижение по ПФ
Rolandnof
servismersedes2.ru/ – Индивидуальный подход к каждому клиенту
MichaelOrdep
https://www.pf-monstr.work – накрутка поведенческих факторов сайта
ElijahNoisT
Non-prescription ED tablets discreetly shipped: Fast-acting ED solution with discreet packaging – Fast-acting ED solution with discreet packaging
Robertgox
viagra 100mg india price SildenaPeak cheapest place to buy viagra
PeterHem
Tadalify: Tadalify – canada cialis for sale
Rolandnof
клубный сервис мерседес москва – доверие клубного обслуживания
MichaelOrdep
https://pf-monstr.work – работа с ПФ
RichardTwero
sildenafil for sale usa: generic viagra cost – SildenaPeak
Rolandnof
https://servismersedes2.ru – Электронный диагностический комплекс STAR
MichaelOrdep
https://pf-monstr.work/ – раскрутка по ПФ
Rolandnof
https://www.servismersedes2.ru/ – Комплексное сервисное сопровождение Mercedes
Danielutina
https://sildenapeak.shop/# SildenaPeak
MichaelOrdep
пф яндекс – базовые решения для Yandex
Rolandnof
https://www.servismersedes2.ru – Элитный техцентр для автомобилей Mercedes-Benz
ElijahNoisT
SildenaPeak: sildenafil sale in india – sildenafil 85
MichaelOrdep
https://www.pf-monstr.work/ – SEO раскрутка по ПФ
Rolandnof
автосервис мерседес москва – оснащенный по последнему слову техники центр
PeterHem
Tadalify: cialis black 800 to buy in the uk one pill – order cialis soft tabs
RichardTwero
viagra tablets for men: SildenaPeak – SildenaPeak
MichaelOrdep
[url=https://pf-monstr.work/]pf-monstr.work[/url] – работа с ПФ
Rolandnof
http://servismersedes2.ru/ – Профессиональный подход к каждому автомобилю
Robertgox
SildenaPeak SildenaPeak SildenaPeak
Rolandnof
servismersedes2.ru/ – Обслуживание премиум-салона и комфорт-систем
MichaelOrdep
pf-monstr.work/ – накрутка ПФ
Rolandnof
servismersedes2.ru/ – Индивидуальный сервис для каждого автомобиля
MichaelOrdep
https://pf-monstr.work/ – оптимизация поведенческих
Rolandnof
http://servismersedes2.ru/ – Эффективное устранение неисправностей электрооборудования
ElijahNoisT
Men’s sexual health solutions online: Affordable sildenafil citrate tablets for men – Men’s sexual health solutions online
MichaelOrdep
http://pf-monstr.work – накрутка ПФ для проектов и сайтов
PeterHem
Sildenafil oral jelly fast absorption effect: Kamagra oral jelly USA availability – Affordable sildenafil citrate tablets for men
Rolandnof
http://servismersedes2.ru/ – Рабочий веб-адрес сервиса
RichardTwero
Kamagra oral jelly USA availability: Kamagra reviews from US customers – Affordable sildenafil citrate tablets for men
MichaelOrdep
http://pf-monstr.work/ – накрутка ПФ
Rolandnof
http://www.servismersedes2.ru – Надежный ремонт двигателей и трансмиссий
Robertgox
viagra brand price viagra tablets in india fast delivery viagra uk
MichaelOrdep
пф яндекс услуги – полный спектр услуг для продвижения
Rolandnof
servismersedes2.ru – Капитальный ремонт силовых агрегатов
Danielutina
http://kamameds.com/# Non-prescription ED tablets discreetly shipped
Rolandnof
http://servismersedes2.ru – Круглосуточная техническая поддержка
MichaelOrdep
pf-monstr.work – SEO продвижение по ПФ
ElijahNoisT
SildenaPeak: SildenaPeak – viagra pills for sale
Rolandnof
servismersedes2.ru/ – Корректный URL для ввода в браузере
MichaelOrdep
https://pf-monstr.work/ – поведенческие факторы улучшение
RichardTwero
tadalafil cheapest online: tadalafil canada is it safe – Tadalify
PeterHem
sildenafil over the counter australia: viagra price pfizer – can you buy genuine viagra online
Rolandnof
servismersedes2.ru – Специализированный центр с оригинальными запчастями
MichaelOrdep
https://pf-monstr.work/ – улучшение ПФ
Rolandnof
https://servismersedes2.ru – Ремонт мультиконтурных сидений
MichaelOrdep
pf-monstr.work – накрутка ПФ и улучшение
Rolandnof
https://servismersedes2.ru – Гарантийное обслуживание с официальной документацией
Michaelfar
IverGrove IverGrove IverGrove
MichaelOrdep
http://pf-monstr.work – накрутка ПФ для сайтов и проектов
Rolandnof
ремонт mercedes – качественное устранение любых неполадок
FrankFak
prednisone 15 mg tablet: prednisone cream brand name – prednisone cream brand name
WayneUndiz
SteroidCare Pharmacy: SteroidCare Pharmacy – prednisone 10mg tablets
JerryRek
buy amoxicillin over the counter uk: amoxicillin 500 mg online – buy amoxicillin canada
Rolandnof
http://servismersedes2.ru – Беспрецедентное внимание к деталям ремонта
MichaelOrdep
сервис поведенческих факторов – факторные сервисы
Rolandnof
https://www.servismersedes2.ru/ – Индивидуальный подход к каждому автомобилю
MichaelOrdep
https://pf-monstr.work – накрутка ПФ для сайтов
Rolandnof
https://servismersedes2.ru/ – Квалифицированное обслуживание трансмиссии
MichaelOrdep
http://www.pf-monstr.work – раскрутка сайта по ПФ
WayneUndiz
CardioMeds Express: lasix 40mg – lasix 100 mg tablet
FrankFak
IverGrove: IverGrove – where can i buy ivermectin for humans
Rolandnof
то мерседес – регламентное техническое обслуживание
Michaelfar
ivermectin covid 19 uptodate IverGrove IverGrove
JerryRek
TrustedMeds Direct: TrustedMeds Direct – buy amoxicillin online no prescription
MichaelOrdep
http://www.pf-monstr.work – улучшение ПФ
Rolandnof
[url=https://servismersedes2.ru/]http://www.servismersedes2.ru[/url] – Альтернативный адрес в сети
MichaelOrdep
https://www.pf-monstr.work/ – раскрутка по ПФ
Rolandnof
https://servismersedes2.ru/ – Современное оборудование для точной диагностики
Rolandnof
servismersedes2.ru – Качественный ремонт двигателей любой сложности
MichaelOrdep
http://pf-monstr.work – накрутка ПФ для проектов
WayneUndiz
CardioMeds Express: lasix pills – furosemide
JerryRek
CardioMeds Express: furosemide – lasix 100 mg
Rolandnof
https://servismersedes2.ru/ – Профессиональное обслуживание роботизированных коробок
MichaelOrdep
яндекс пф – проверенные методы
FrankFak
online order prednisone 10mg: buy prednisone online canada – prednisone pharmacy prices
Rolandnof
ремонт mercedes в москве – большой опыт работы с маркой
MichaelOrdep
http://www.pf-monstr.work – раскрутка по ПФ
DavidUtilk
https://ivergrove.com/# IverGrove
Rolandnof
ремонт мерседес бенц в москве – минимальные сроки выполнения работ
WayneUndiz
generic amoxicillin cost: TrustedMeds Direct – amoxicillin 500mg pill
MichaelOrdep
https://pf-monstr.work – оптимизация ПФ
Rolandnof
http://servismersedes2.ru – Беспрецедентное внимание к деталям ремонта
JerryRek
ivermectin 24 mg: how much ivermectin to give a dog for worms – ivermectin fda label
MichaelOrdep
накрутка пф заказать в спб – питерское решение
Rolandnof
http://servismersedes2.ru – Замена систем адаптивного освещения
FrankFak
prednisone 30 mg: SteroidCare Pharmacy – where to buy prednisone 20mg no prescription
Rolandnof
http://www.servismersedes2.ru – Ювелирная настройка адаптивной подвески
MichaelOrdep
https://pf-monstr.work – SEO раскрутка по ПФ
Rolandnof
диагностика мерседес в москве – глубокая диагностика неисправностей
MichaelOrdep
https://www.pf-monstr.work – работа с поведенческими факторами
WayneUndiz
FertiCare Online: how to get generic clomid online – FertiCare Online
Rolandnof
servismersedes2.ru – Компьютеризированная диагностика инжекторных систем
JerryRek
where can i buy cheap clomid without a prescription: FertiCare Online – can i get clomid price
MichaelOrdep
pf-monstr.work – улучшение ПФ
Rolandnof
http://www.servismersedes2.ru – Диагностика электронных систем любой сложности
FrankFak
ivermectin for humans: IverGrove – ivermectin 6 mg walgreens
MichaelOrdep
[url=https://pf-monstr.work/]pf-monstr.work[/url] – накрутка ПФ для бизнеса и проектов
Rolandnof
автосервис мерседес – широкий спектр услуг для Mercedes-Benz
DavidUtilk
http://ferticareonline.com/# FertiCare Online
Rolandnof
servismersedes2.ru/ – Индивидуальные решения для сложных технических задач
WayneUndiz
IverGrove: IverGrove – IverGrove
JerryRek
ivermectin plus: ivermectin 0.5% lotion – how expensive is ivermectin
Rolandnof
http://www.servismersedes2.ru – Глубокая диагностика всех систем автомобиля
Rolandnof
мерседес сервис – сертифицированные мастера
FrankFak
lasix generic name: furosemide 100 mg – lasix generic name
Michaelfar
SteroidCare Pharmacy SteroidCare Pharmacy prednisone 10
WayneUndiz
CardioMeds Express: CardioMeds Express – generic lasix
JerryRek
CardioMeds Express: lasix tablet – CardioMeds Express
FrankFak
FertiCare Online: FertiCare Online – can i buy cheap clomid for sale
DavidUtilk
http://trustedmedsdirect.com/# can you purchase amoxicillin online
Michaelfar
IverGrove IverGrove stromectol tablets buy online
WayneUndiz
ivermectin for covid treatment: IverGrove – topical ivermectin for ear mites in cats
JerryRek
TrustedMeds Direct: buy cheap amoxicillin – price of amoxicillin without insurance
Jamalamupt
farmaci senza ricetta elenco FarmaciDiretti migliori farmacie online 2024
Kennethsweet
viagra consegna in 24 ore pagamento alla consegna: PotenzaFacile – siti sicuri per comprare viagra online
Ronaldcak
comprare farmaci online all’estero: trattamenti per la salute sessuale senza ricetta – comprare farmaci online con ricetta
Eddieviozy
http://pillolesubito.com/# acquisto farmaci con ricetta
RobertLoche
farmacie online affidabili: Farmacia online miglior prezzo – farmacia online
Jamalamupt
acquistare farmaci senza ricetta kamagra online Italia п»їFarmacia online migliore
Kennethsweet
farmacia online piГ№ conveniente: kamagra originale e generico online – Farmacie online sicure
Ronaldcak
farmaci senza ricetta elenco: sildenafil generico senza ricetta – Farmacie on line spedizione gratuita
RobertLoche
viagra generico sandoz: le migliori pillole per l’erezione – viagra online consegna rapida
Eddieviozy
https://farmacidiretti.shop/# Farmacia online miglior prezzo
Jamalamupt
farmacia senza ricetta recensioni pillole per la disfunzione erettile in Italia miglior sito dove acquistare viagra
Kennethsweet
cialis farmacia senza ricetta: viagra online Italia – viagra generico sandoz
Ronaldcak
Farmacia online più conveniente: farmaci generici a prezzi convenienti – farmacie online sicure
RobertLoche
viagra generico prezzo piГ№ basso: gel per erezione in farmacia – viagra generico sandoz
Jamalamupt
viagra prezzo farmacia 2023 viagra subito siti sicuri per comprare viagra online
Ronaldcak
viagra acquisto in contrassegno in italia: farmacia online sildenafil Italia – gel per erezione in farmacia
RobertLoche
farmacie online affidabili: accesso rapido a cialis generico online – acquisto farmaci con ricetta
Eddieviozy
https://pillolesubito.com/# farmacia online
Kennethsweet
viagra online spedizione gratuita: acquistare viagra generico online – viagra 50 mg prezzo in farmacia
Jamalamupt
farmacie online affidabili consegna rapida in tutta Italia Farmacie on line spedizione gratuita
RobertLoche
acquistare farmaci senza ricetta: farmacia online cialis Italia – comprare farmaci online all’estero
HaroldGlits
MapleMeds Direct: MapleMeds Direct – MapleMeds Direct
KennethbiawL
real mexican pharmacy USA shipping BorderMeds Express trusted mexico pharmacy with US shipping
Anthonyarize
BorderMeds Express: mexican pharmacy for americans – BorderMeds Express
PatrickSat
https://bordermedsexpress.com/# medicine in mexico pharmacies
RichardHic
BharatMeds Direct: india online pharmacy – india pharmacy
HaroldGlits
MapleMeds Direct: MapleMeds Direct – america rx pharmacy
KennethbiawL
BorderMeds Express buy cheap meds from a mexican pharmacy BorderMeds Express
Anthonyarize
viagra pills from mexico: online mexico pharmacy USA – amoxicillin mexico online pharmacy
RichardHic
propecia usa pharmacy: MapleMeds Direct – MapleMeds Direct
HaroldGlits
BorderMeds Express: mexican drugstore online – BorderMeds Express
PatrickSat
https://maplemedsdirect.shop/# internet viagra pharmacy
KennethbiawL
MapleMeds Direct MapleMeds Direct revive rx pharmacy
RichardHic
п»їlegitimate online pharmacies india: BharatMeds Direct – Online medicine order
Anthonyarize
BorderMeds Express: BorderMeds Express – buy antibiotics from mexico
HaroldGlits
mexico pharmacies prescription drugs: mexican pharmaceuticals online – mexico drug stores pharmacies
AndrewPoeby
stroyexpertsochi.ru/ Проверяйте stroyexpertsochi.ru/ и получите практические советы по проектированию и благоустройству территории.
KennethbiawL
buy cialis from mexico gabapentin mexican pharmacy get viagra without prescription from mexico
RichardHic
trusted mexican pharmacy: BorderMeds Express – BorderMeds Express
Anthonyarize
BharatMeds Direct: BharatMeds Direct – Online medicine home delivery
AndrewPoeby
строительство дома в сочи советы Следуйте важными советами по строительству дома в Сочи и обеспечьте качественности вашего дома.
PatrickSat
http://maplemedsdirect.com/# buy adipex online pharmacy
AndrewPoeby
технологии сейсмоустойчивого строительства Сочи Используйте технологии сейсмоустойчивого строительства в Сочи и обеспечьте безопасность вашего строения.
HaroldGlits
purple pharmacy mexico price list: BorderMeds Express – medication from mexico pharmacy
Jamespug
зелёный дом с солнечными панелями Сочи Используйте зелёный дом с солнечными панелями и экономьте деньги.
RichardHic
BharatMeds Direct: cheapest online pharmacy india – Online medicine order
KennethbiawL
MapleMeds Direct provigil mexico pharmacy MapleMeds Direct
Jamespug
укрепление склона сочи Выбирайте укрепление склона и обеспечьте надежность участка.
Anthonyarize
BorderMeds Express: BorderMeds Express – BorderMeds Express
Jamespug
строительство дома под ключ Сочи с гарантией Выбирайте строительство дома под ключ Сочи с гарантией и гарантируйте качественный дом.
Jamespug
ландшафтный дизайн с террасированием Сочи Следуйте ландшафтный дизайн с террасированием Сочи и гарантируйте красоту.
Jamespug
строительство дома в сочи советы Выбирайте строительство дома в Сочи советы и получите долговечность дома.
HaroldGlits
Female Viagra: kamagra oral jelly – MapleMeds Direct
RichardHic
top 10 pharmacies in india: BharatMeds Direct – top 10 pharmacies in india
Jamespug
https://stroyexpertsochi.ru/ Узнайте на наш сайт и узнайте о способах защиты стен от грибка и антикоррозийной обработке металлоконструкций.
KennethbiawL
online pharmacy india BharatMeds Direct indian pharmacy paypal
Anthonyarize
BorderMeds Express: BorderMeds Express – BorderMeds Express
Jamespug
http://www.stroyexpertsochi.ru Ознакомьтесь с наши проекты и получите ценные советы по строительству домов и коттеджей в Сочи.
Jamespug
https://www.stroyexpertsochi.ru/ Посетите раздел “Отзывы клиентов” и узнайте о зеленых домах, экодомах и установке солнечных панелей.
Jamespug
stroyexpertsochi.ru/ Проверяйте портфолио объектов и ознакомьтесь с ландшафтным дизайном и террасированием участков.
PatrickSat
https://bordermedsexpress.shop/# BorderMeds Express
HaroldGlits
pharmacy online 365 legit: MapleMeds Direct – MapleMeds Direct
RichardHic
legit mexico pharmacy shipping to USA: order from mexican pharmacy online – cheap mexican pharmacy
Jamespug
http://stroyexpertsochi.ru Откройте наш каталог решений и ознакомьтесь с секретами строительства дома в Сочи и Краснодарском крае.
Sunny
online uk bingo reviews, gambling stocks in united states and no deposit free bonus spins usa aug, 28,2021, or bingo no deposit bonus roll to win craps cherokee
(Nestor) real money united states
KennethbiawL
legitimate online pharmacy no prescription world pharmacy rx MapleMeds Direct
Jamespug
http://www.stroyexpertsochi.ru Просмотрите наши проекты и узнайте обо всех тонкостях фундамента, дренажных систем и сейсмоустойчивых технологий.
Anthonyarize
MapleMeds Direct: MapleMeds Direct – MapleMeds Direct
Jamespug
https://www.stroyexpertsochi.ru/ Ознакомьтесь с раздел “Отзывы клиентов” и изучите современные методы строительства в Краснодарском крае и Сочи.
💾 🚀 Quick Transfer: 0.35 BTC received. Confirm here > https://graph.org/GET-FREE-BITCOIN-07-23?hs=820eb006fb1b72e7abbb4da4628f6b6d& 💾
fixzn0
Jamespug
http://stroyexpertsochi.ru/ Изучите раздел услуг и ознакомьтесь с технологиями сейсмоустойчивого строительства и защиты от дождей.
lecheniekrasnodarelusa
вывод из запоя круглосуточно
narkolog-krasnodar011.ru
вывод из запоя
vivodkrasnoyarskelusa
Срочная помощь при запое: капельница на дому в Красноярске Проблема алкогольной зависимости требует квалифицированного подхода. При запойном состоянии наблюдаются тяжелые симптомы‚ такие как тремор‚ повышенная потливость‚ беспокойство и‚ порой‚ галлюцинации. В таких случаях нужна помощь нарколога‚ который обеспечит медицинскую поддержку. Преимущества домашней терапии заключаются в том‚ что пациент находится в знакомой среде‚ что помогает быстрее восстановиться после запоя. Не менее важно уделить внимание профилактике рецидивов‚ чтобы предотвратить повторные запои. При обращении к специалистам вы получите не только капельницы для детоксикации‚ но и всестороннее лечение алкоголизма‚ которое поможет вам полностью восстановиться.
Jamespug
http://stroyexpertsochi.ru/ Проверяйте раздел услуг и получите практические советы по строительству частного дома под ключ и отделке коттеджей.
RichardHic
viagra pills from mexico: rybelsus from mexican pharmacy – BorderMeds Express
lecheniekrasnodarelusa
вывод из запоя
narkolog-krasnodar011.ru
вывод из запоя круглосуточно краснодар
HaroldGlits
indian pharmacy online: BharatMeds Direct – india online pharmacy
Jamespug
https://stroyexpertsochi.ru/ Погрузитесь в наш сайт и узнайте о фундаменте, дренажных системах и сейсмоустойчивых технологиях.
KennethbiawL
BharatMeds Direct best india pharmacy BharatMeds Direct
Anthonyarize
BorderMeds Express: buy from mexico pharmacy – BorderMeds Express
Jamespug
stroyexpertsochi.ru/ Проверяйте портфолио объектов и узнайте о лучших материалах для строительства в Сочи.
vivodzapojkrasnodarelusa
экстренный вывод из запоя
narkolog-krasnodar012.ru
вывод из запоя круглосуточно краснодар
narkologiyakrasnoyarskelusa
Облегчение состояния после запоя в домашних условиях требует комплексного подхода. Прежде всего, важно помнить о детоксикации организма. Употребление большого количества воды способствует выведению токсинов. Народные методы борьбы с запоем, такие как настои из трав (мелисса, мяты), могут уменьшить дискомфорт. вывод из запоя круглосуточно Красноярск Возвращение к нормальной жизни после запоя включает здоровое питание, фрукты и овощи ускоряют процесс. Поддержка близких играет ключевую роль, так как поддержка близких может помочь избежать новых запоев.
Jamespug
http://www.stroyexpertsochi.ru Узнайте больше на наши проекты и ознакомьтесь с современными методами благоустройства участка и геопластики.
narkologiyakrasnodarelusa
вывод из запоя
narkolog-krasnodar012.ru
вывод из запоя
Jamespug
http://www.stroyexpertsochi.ru Узнайте больше на наши проекты и узнайте обо всех тонкостях фундамента, дренажных систем и сейсмоустойчивых технологий.
RichardHic
BharatMeds Direct: online pharmacy india – BharatMeds Direct
lecheniekrasnodarelusa
лечение запоя краснодар
narkolog-krasnodar013.ru
вывод из запоя цена
HaroldGlits
medication from mexico pharmacy: mexican mail order pharmacies – mexico drug stores pharmacies
Jamespug
https://www.stroyexpertsochi.ru Загляните на материалы и узнайте, как правильно выбрать материалы для влажного климата.
PatrickSat
http://bharatmedsdirect.com/# BharatMeds Direct
KennethbiawL
BharatMeds Direct BharatMeds Direct BharatMeds Direct
Jamespug
http://www.stroyexpertsochi.ru Просмотрите наш сайт и узнайте о монтаже фундаментов разных типов и их особенностях.
Nola
united kingdom pokies online real money, no deposit bonus codes usa
and free spins 2021 and spin palace mobile casino australia, or casino online
united kingdom free
Here is my webpage; who wears baccarat rouge 540, Stephanie,
Anthonyarize
BorderMeds Express: BorderMeds Express – BorderMeds Express
izzapoyakrasnodarelusa
вывод из запоя краснодар
narkolog-krasnodar013.ru
вывод из запоя
Jamespug
https://www.stroyexpertsochi.ru/ Откройте раздел “Отзывы клиентов” и изучите современные методы строительства в Краснодарском крае и Сочи.
zapojkrasnodarelusa
экстренный вывод из запоя
narkolog-krasnodar014.ru
вывод из запоя цена
Jamespug
http://www.stroyexpertsochi.ru Посетите наш сайт и получите рекомендации по сейсмоустойчивому строительству и безопасности семьи.
Miltonlef
Book of Ra Deluxe slot online Italia: migliori casino online con Book of Ra – migliori casino online con Book of Ra
vivodsmolenskelusa
вывод из запоя круглосуточно смоленск
vivod-iz-zapoya-smolensk013.ru
вывод из запоя круглосуточно смоленск
Jamespug
https://stroyexpertsochi.ru/ Зайдите на наш сайт и узнайте обо всех тонкостях строительства в Сочи и Краснодарском крае.
vivodzapojkrasnodarelusa
лечение запоя
narkolog-krasnodar015.ru
лечение запоя
vivodzapojkrasnodarelusa
вывод из запоя краснодар
narkolog-krasnodar014.ru
лечение запоя
Jamespug
http://stroyexpertsochi.ru/ Исследуйте раздел услуг и ознакомьтесь с технологиями сейсмоустойчивого строительства и защиты от дождей.
RamonVekly
promosi dan bonus harian preman69: promosi dan bonus harian preman69 – preman69 slot
AaronJet
bonaslot bonaslot link resmi mudah diakses bonaslot login
alkogolizmsmolenskelusa
лечение запоя смоленск
vivod-iz-zapoya-smolensk014.ru
лечение запоя
Jamespug
https://stroyexpertsochi.ru/ Узнайте на наш сайт и получите информацию о зелёных домах, экодомах и инновационных материалах.
LouisWhemy
garuda888 live casino Indonesia: 1win888indonesia – link alternatif garuda888 terbaru
Jamespug
https://stroyexpertsochi.ru/ Просмотрите наш сайт и ознакомьтесь с современными решениями для ландшафтного дизайна и террасирования.
Miltonlef
bonus di benvenuto per Book of Ra Italia: giri gratis Book of Ra Deluxe – recensioni Book of Ra Deluxe slot
zapojtulaelusa
Специалисты нашей команды оказывают срочную помощь и советы, чтобы сделать процесс вывода из запоя безопасным и удобным. Мы знаем, насколько важна поддержка со стороны близких в это непростое время, в связи с этим предлагаем анонимное лечение и реабилитацию пациентов. Обращайтесь на narkolog-tula015.ru для получения наркологической помощи и восстановления после запоя. Мы здесь, чтобы помочь вам в любое время.
alkogolizmkrasnodarelusa
вывод из запоя
narkolog-krasnodar015.ru
лечение запоя
AlfredJag
https://1wbona.shop/# bonaslot
Jamespug
https://www.stroyexpertsochi.ru Зайдите на материалы и получите информацию о водостойкой штукатурке и антикоррозийной обработке металлоконструкций.
narkologiyasmolenskelusa
экстренный вывод из запоя смоленск
vivod-iz-zapoya-smolensk015.ru
вывод из запоя
Jamespug
https://www.stroyexpertsochi.ru Ознакомьтесь с материалы и познакомьтесь с полным спектром услуг по строительству и ремонту домов.
RamonVekly
garuda888 slot online terpercaya: link alternatif garuda888 terbaru – permainan slot gacor hari ini
narkologiyatulaelusa
Вызов нарколога в Тулу — это первый шаг к восстановлению. Профессиональные наркологические услуги, направленные на безопасный вывод из запоя, гарантируют нужную медицинскую помощь. Профессиональный нарколог проводит детоксикацию организма, что критически важно для здоровья пациента. Лечение алкоголизма подразумевает индивидуальный подход, что увеличивает вероятность успешного выздоровления. вызов нарколога тула Недостаточно лишь медицинских процедур для помощи при запое. Врач-нарколог предоставляет консультацию для определения следующих шагов, включая реабилитацию зависимых. Вызов специалиста на дом делает процесс менее стрессовым и более комфортным. Заботьтесь о своем здоровье и не откладывайте обращение за помощью!
Jamespug
stroyexpertsochi.ru/ Просмотрите портфолио объектов и узнайте о зеленых домах, экодомах и солнечных панелях.
AaronJet
garuda888 live casino Indonesia garuda888 live casino Indonesia permainan slot gacor hari ini
vivodzapojtulaelusa
Капельницы для вывода из запоя — важный элемент лечения алкоголизма при лечении алкоголизма. При этом следует учитывать юридические аспекты, связанные с правами пациентов и обязанностями медицинского персонала. Ключевое значение является согласие пациента на терапию, что является краеугольным камнем медицинской этики. вывод из запоя В процессе оказания наркологической помощи крайне важно следовать правовым стандартам, обеспечивая защиту прав пациентов. Клинические рекомендации обращают внимание на важность индивидуального подхода к каждому случаю запоя. Помощь в лечении включает социальные услуги, направленные на реабилитацию. Ответственность врачей за качество лечения алкоголизма также не должна быть забыта. Крайне важно, чтобы вывод из запоя проходил безопасно и эффективно, что подразумевает высокий уровень профессионализма и строгого соблюдения норм.
Jamespug
http://stroyexpertsochi.ru Просмотрите наш каталог решений и изучите эффективные дренажные системы и подпорные стенки.
vivodkrasnoyarskelusa
Капельница – это важная процедура, которая помогает скорейшему восстановлению физического состояния человека, страдающего алкогольную зависимость. В Красноярске вызов нарколога для проведения этой процедуры оказывается всё более актуальным. Алкоголь негативно сказывается на организм, вызывая симптомам похмелья, такими как мигрень, тошнота и слабость.Лечение алкоголизма включает detox, который помогает очищению организма от токсинов. Капельница обеспечивает поступление жизненно важных веществ, улучшая состояние пациента. Нарколог предоставляет медицинскую помощь при запое, что позволяет избежать серьёзных осложнений. вызов нарколога Красноярск Восстановление организма после запоя нуждается в комплексном подходе, включая реабилитацию от алкоголя. Лечение запоя может включать как медикаментозные методы, так и психотерапевтическую помощь. Важно помнить, что здоровье – это главное, и оперативная помощь нарколога может спасти жизнь.
Jamespug
http://www.stroyexpertsochi.ru Откройте наши проекты и получите ценные советы по строительству домов и коттеджей в Сочи.
Miltonlef
Book of Ra Deluxe soldi veri: book of ra deluxe – giri gratis Book of Ra Deluxe
Jamespug
строительство и проектирование дома Сочи Применяйте строительством и проектированием дома Сочи и обеспечьте удобство.
alkogolizmtulaelusa
Обращение к наркологу на дом в конфиденциальном порядке – это важный шаг для людей, страдающих от наркозависимости. Профессиональная помощь нарколога на дому дают возможность обеспечить профессиональную помощь в комфортной и безопасной обстановке. Нарколог, работающий анонимно проведет консультацию, оценит состояние пациента и разработает лечение наркомании на дому. Это может включать психотерапевтическую помощь и поддержку зависимого человека. Срочный вызов нарколога также возможен, что является крайне важным в критических ситуациях. Услуги нарколога включает профилактические меры против зависимости и реабилитацию наркоманов, обеспечивая конфиденциальное лечение и надежность процесса. narkolog-tula017.ru
Jamespug
[url=https://stroyexpertsochi.ru/]stroyexpertsochi.ru[/url] Посетите наши материалы и получите информацию о ландшафтном дизайне и террасировании участка.
LouisWhemy
bonaslot link resmi mudah diakses: bonaslot – bonaslot situs bonus terbesar Indonesia
zapojkrasnoyarskelusa
Частный нарколог на дому в Красноярске предоставляет незаменимую поддержку тем, кто борется с зависимостями. Процесс лечения зависимостей может быть сложным процессом, но выездной нарколог предлагает комфортные условия и конфиденциальность. На сайте vivod-iz-zapoya-krasnoyarsk011.ru можно назначить встречу с наркологом, который приедет к вам домой. На дому пациентам предоставляется медицинская помощь включает детоксикацию организма и психологическую терапию для борьбы с зависимостями, что позволяет пациенту сделать первые шаги к свободе от наркотиков или алкоголя. Программа реабилитации разрабатывается с индивидуальным подходом, что позволяет учитывать уникальные потребности каждого пациента. Поддержка родственников играет важнейшую роль в предотвращении рецидивов. Выездной нарколог обеспечивает не только медицинскую помощь, но и эмоциональную поддержку, что важно для успешной реабилитации наркоманов и помощи при алкоголизме.
izzapoyatulaelusa
Капельница при похмелье – данный метод является эффективным способом лечения, который помогает устранить симптомы алкогольной интоксикации. Состояние похмелья сопровождается недостатком жидкости, что проявляется болью в голове, тошнотой и общей слабостью. Капельница включает глюкозу и электролиты, которые возвращают баланс жидкости в организме. Лечение похмелья с помощью капельницы позволяет быстро устранить симптомы, обеспечивая очищение организма. Внутривенное введение жидкости ускоряет процесс восстановления. Капельница в домашних условиях также может быть полезна, но требуется медицинская помощь для правильного подбора компонентов. Существуют и народные средства: травы от похмелья, например, мяту или зверобой, которые помогают улучшить состояние. Однако капельница остается наиболее эффективным методом облегчить недомогание после пьянки. На сайте narkolog-tula016.ru можно найти информацию о различных вариантах капельниц и их воздействии на организм.
Jamespug
http://www.stroyexpertsochi.ru Просмотрите наш сайт и ознакомьтесь с экологичными строительными материалами и энергосберегающими решениями.
RamonVekly
preman69 slot: preman69 – preman69 login tanpa ribet
Jamespug
stroyexpertsochi.ru Погрузитесь в наши материалы и получите максимум информации о фундаменте, бетонных и монолитных конструкциях.
vivodtulaelusa
ДОСТУПНЫЙ ВЫВОД ИЗ ЗАПОЯ В ТУЛЕ: РЕАЛЬНОСТЬ И МИФЫ Процесс лечения алкоголизма является непростым и требует комплексного подхода. В Туле множество наркологических клиник предлагают лечение запоя и реабилитацию от запоя, однако имеются ложные представления о лечении алкоголизма, которые могут сбивать с толку. Во-первых, некоторые люди полагают, что вывод из запоя – это быстрое мероприятие. На самом деле, реальные методы вывода из запоя, такие как детоксикация и психотерапия, требуют определенного времени. Наркологическая клиника Тула в Туле предлагает программы реабилитации, в рамках которых специалисты оказывают помощь в восстановлении после запоя. Важно отметить, что психотерапия при зависимости играет ключевую роль. Консультация нарколога способствует выявлению причин зависимости и созданию индивидуального плана лечения. Не стоит забывать, что в Туле лечение зависимости доступно и эффективно, при условии своевременного обращения за помощью.
AaronJet
Starburst slot online Italia casino online sicuri con Starburst starburst
Jamespug
http://www.stroyexpertsochi.ru Зайдите на наш сайт и получите информацию о геопластике участка и оптимальном использовании пространства.
Miltonlef
bonaslot login: bonaslot kasino online terpercaya – bonaslot jackpot harian jutaan rupiah
vivodzapojkrasnoyarskelusa
Прокапаться в Красноярске — это серьезный вопрос‚ требующая профессионального подхода. На сайте vivod-iz-zapoya-krasnoyarsk012.ru вы можете найти предложения по водоснабжению‚ включая установку и починку различных систем. Наша команда сантехников готова предоставить качественные услуги и быструю диагностику. Мы понимаем‚ что вызов специалиста может потребоваться в экстренной ситуации‚ поэтому готовы предложить акционные предложения. Мы гордимся отзывами наших клиентов, которые подтверждают высокий уровень нашей работы. Ремонт и установка сантехники — это то, что мы делаем лучше всего‚ и мы обеспечиваем выполнение работы на высшем уровне.
Jamespug
http://www.stroyexpertsochi.ru Зайдите наши проекты и получите максимум информации о проектировании и строительстве частного дома под ключ.
AlfredJag
https://1win69.shop/# promosi dan bonus harian preman69
zapojtulaelusa
Нарколог — это медицинский работник, который обеспечивает поддержку людям, испытывающим проблемы от алкоголизма и наркомании. Лечение зависимостей включает в себя очистку организма, медикаменты и психотерапию. Необходимо получить консультацию нарколога для разработки персонализированного подхода реабилитации. Поддержка родственников играет ключевую роль в выздоровлении, а группы взаимопомощи помогают адаптироваться в социальной среде. Профилактика зависимостей также имеют значение, чтобы предотвратить рецидивы. Консультация с профессионалами на narkolog-tula017.ru обеспечит высококачественную помощь и поддержку на каждом этапе лечения.
Jamespug
http://stroyexpertsochi.ru/ Ознакомьтесь с раздел услуг и получите советы по выбору материалов для морского и влажного климата.
zapojtulaelusa
Медицинские учреждения предлагают восстановление зависимых, которая включает лечение зависимости и консультации психолога. Процедура кодирования также является популярной методом, помогающей снизить желание пить. Круглосуточные клиники обеспечивают анонимное лечение и помощь специалистов, что дает возможность пациентам ощущать комфортно и безопасно. вывод из запоя круглосуточно Адаптация в обществе и поддержка после лечения — необходимые элементы, обеспечивающие успешной реинтеграции в общество. Лечение алкоголизма в Туле становится доступным благодаря различным программам и методикам, которые помогают справиться с этой серьезной проблемы.
Jamespug
https://www.stroyexpertsochi.ru Узнайте больше на материалы и изучите возможности современного ландшафтного дизайна и террасирования.
Jamespug
http://stroyexpertsochi.ru/ Посетите раздел услуг и получите экспертные рекомендации по проектированию и благоустройству территории.
izzapoyasmolenskelusa
лечение запоя
vivod-iz-zapoya-smolensk013.ru
лечение запоя смоленск
RamonVekly
preman69 login: preman69 slot – slot gacor hari ini preman69
AaronJet
giri gratis Book of Ra Deluxe giri gratis Book of Ra Deluxe Book of Ra Deluxe slot online Italia
Jamespug
http://stroyexpertsochi.ru/ Просмотрите раздел услуг и получите советы по выбору материалов для морского и влажного климата.
vivodzapojtulaelusa
Нарколог на дом – это удобное решение для тех, кто сталкивается с алкогольной зависимостью или наркоманией. Лечение наркомании включает в себя очистку организма и восстановление зависимых. Выездной нарколог предоставляет анонимное лечение, что имеет большое значение для пациентов, которые не хотят посещать медицинские учреждения. Кодирование от алкоголизма – проверенный способ, который можно провести на дому. Выездная помощь включает в себя психологическую поддержку и медицинское сопровождение. Консультации специалиста помогут понять, как избавиться от зависимости. Программы восстановления и поддержка семьи играют ключевую роль в процессе лечения. На сайте narkolog-tula020.ru вы найдете подробности о доступных услугах.
lechenietulaelusa
Прокапка после алкогольной зависимости — это важная медицинская процедура , направленная на детоксикацию организма и восстановление здоровья человека. Во время обращения к наркологу для оказания помощи на дому осуществляется введение лекарственных средств через капельницу, что помогает очистить кровь от токсинов , которые накапливаются при злоупотреблении алкоголем. Нарколог на дом срочно В процессе обычно используются солевые растворы, витамины и минералы, что помогает улучшить общее состояние и облегчает симптомы похмелья . Лечение на дому дает возможность пациенту оставаться в знакомой среде, что играет важную роль в процессе реабилитации. Наркологическая помощь включает в себя психологическую и медицинскую поддержку, что значительно увеличивает вероятность успешного восстановления после алкогольной зависимости. Важно следовать советам по лечению и регулярно проходить процедуру прокапки для достижения оптимальных результатов.
Miltonlef
starburst: giocare a Starburst gratis senza registrazione – giocare da mobile a Starburst
Jamespug
http://stroyexpertsochi.ru/ Исследуйте раздел услуг и ознакомьтесь с ландшафтным дизайном, благоустройством участка и геопластикой.
Jamespug
https://www.stroyexpertsochi.ru/ Погрузитесь в раздел “Отзывы клиентов” и узнайте о защите стен от грибка и антикоррозийной обработке металлоконструкций.
izzapoyasmolenskelusa
вывод из запоя смоленск
vivod-iz-zapoya-smolensk014.ru
вывод из запоя
LouisWhemy
bonaslot situs bonus terbesar Indonesia: 1wbona – bonaslot situs bonus terbesar Indonesia
narkologiyatulaelusa
Цены на капельницу от запоя на дому в Туле могут изменяться в зависимости от ряда факторов. Во-первых, стоимость услуг нарколога может различаться в зависимости от опыта врача и репутации медицинского учреждения. Нарколог на выезде предлагает удобство, что также сказывается на стоимости.Кроме того, тип капельницы и её компоненты (например, глюкоза, витамины) также влияют на цену. Обычно, цена капельницы включает медицинскую помощь на дому, что добавляет к общим расходам.Услуги наркологии, такие как лечение алкогольной зависимости и реабилитация при запое, могут различаться по стоимости в зависимости от длительности и сложности лечения. Необходимо учитывать, что первый шаг в борьбе с алкогольной зависимостью требует квалифицированной поддержки и комплексного подхода. нарколог на дом Если вы ищете помощь при запое, рекомендуется обратиться к специалистам, которые могут предоставить актуальную информацию о ценах и услугах. В Туле услуги наркологии предлагают разнообразные решения для восстановления здоровья и улучшения качества жизни.
Jamespug
http://www.stroyexpertsochi.ru Посетите наши проекты и узнайте обо всех секретах строительства и особенностях климата Сочи и Краснодарского края.
alkogolizmtulaelusa
Наркология на дом: забота о здоровье и помощь
Jamespug
строительство коттеджа с отделкой под ключ Следуйте строительство коттеджа с отделкой под ключ и гарантируйте надежность вашего строения.
RamonVekly
Starburst giri gratis senza deposito: bonus di benvenuto per Starburst – casino online sicuri con Starburst
Jamespug
ландшафтный дизайн с террасированием Сочи Используйте ландшафтный дизайн с террасированием и эффектно обустраивайте участок.
AaronJet
bonaslot login bonaslot link resmi mudah diakses bonaslot situs bonus terbesar Indonesia
vivodsmolenskelusa
лечение запоя
vivod-iz-zapoya-smolensk015.ru
экстренный вывод из запоя смоленск
pansimskelusa
пансионат для престарелых
pansionat-msk007.ru
частный дом престарелых
Miltonlef
giocare da mobile a Starburst: starburst – Starburst slot online Italia
Jamespug
[url=https://stroyexpertsochi.ru/]как построить дом в сочи[/url] Применяйте как построить дом в Сочи и гарантируйте надёжное жильё.
Jamespug
https://stroyexpertsochi.ru/ Исследуйте наш сайт и ознакомьтесь с современными методами террасирования участка и укрепления склона.
vivodtulaelusa
Запой – это серьезное состояние‚ требующее экстренного вмешательства и поддержки. Народные средства часто воспринимаются как эффективные методы лечения‚ но вокруг них существует множество мифов. Например‚ многие думают‚ что лекарственные растения способны быстро снять симптомы запоя. Однако реальность таковы‚ что народные рецепты могут лишь способствовать восстановлению после запоя‚ но не заменить профессиональную реабилитацию от алкоголя. Существует несколько признанных методов‚ среди которых детоксикация и терапия зависимости. Психология зависимости играет ключевую роль в реабилитации. Важно понимать‚ что экстренный вывод из запоя требует системного подхода‚ включающего медикаментозное лечение и поддержку близких. Не стоит полагаться только на народные средства — это может привести к ухудшению состояния.
AlfredJag
https://1wbona.com/# bonaslot kasino online terpercaya
Jamespug
https://www.stroyexpertsochi.ru/ Посетите раздел “Отзывы клиентов” и узнайте о теплоизоляции, энергоэффективных окнах и дверях.
LouisWhemy
bonus di benvenuto per Starburst: Starburst slot online Italia – giocare a Starburst gratis senza registrazione
pansionatmskelusa
пансионат для престарелых людей
pansionat-msk008.ru
дом престарелых
Jamespug
http://stroyexpertsochi.ru Проверьте наш каталог решений и получите практические советы по проектированию и благоустройству территории.
Jamespug
stroyexpertsochi.ru Посетите наши материалы и узнайте о способах энергоэффективного обустройства коттеджей и частных домов.
RamonVekly
preman69 situs judi online 24 jam: slot gacor hari ini preman69 – preman69
izzapoyatulaelusa
Капельное лечение запоя — важный шаг в борьбе с алкоголизмом. Подготовка к процедуре включает несколько шагов. Во-первых, важно вызвать нарколога на дом круглосуточно для получения профессиональной помощи. Врач проведет осмотр и оценит симптомы запоя. Перед капельницей необходимо обеспечить пациента чистой водой и легкой пищей. Это способствует снижению риска осложнений. Важно внимательно ухаживать за пациентом: обеспечьте спокойную обстановку. Нарколог на дом круглосуточно В процессе капельницы важно следить за состоянием пациентачтобы обеспечить его безопасность. После детоксикации организма потребуется психотерапия при запое. Не забывайтечто круглосуточная поддержка нарколога обеспечит успешное лечение запойного состояния.
Jamespug
http://stroyexpertsochi.ru/ Ознакомьтесь с раздел услуг и узнайте, как строить дома в Сочи с учетом влажного климата.
AaronJet
slot gacor hari ini preman69 preman69 preman69 login
pansimskelusa
пансионат для лежачих после инсульта
pansionat-msk009.ru
пансионат для пожилых в москве
Miltonlef
book of ra deluxe: migliori casino online con Book of Ra – migliori casino online con Book of Ra
Jamespug
http://www.stroyexpertsochi.ru Узнайте больше на наш сайт и узнайте лучшие способы строительства дома в Сочи.
Jamespug
http://stroyexpertsochi.ru Погрузитесь в наш каталог решений и получите советы по строительству коттеджей и домов под ключ.
pansmskelusa
пансионат для пожилых с инсультом
pansionat-msk007.ru
дом престарелых в москве
Jamespug
http://stroyexpertsochi.ru/ Посетите раздел услуг и получите советы по выбору материалов для морского и влажного климата.
LouisWhemy
migliori casino online con Book of Ra: Book of Ra Deluxe soldi veri – Book of Ra Deluxe slot online Italia
pansitulaelusa
частные пансионаты для пожилых в туле
pansionat-tula007.ru
пансионат с деменцией для пожилых в туле
Jamespug
stroyexpertsochi.ru Ознакомьтесь с наши материалы и узнайте обо всех тонкостях строительства в Сочи и Краснодарском крае.
internetfrofs
проверить провайдера по адресу
inernetvkvartiru-ekaterinburg004.ru
провайдеры по адресу
Jamespug
stroyexpertsochi.ru Посетите наши материалы и получите советы по строительству частного дома с учётом особенностей местности.
RamonVekly
garuda888 slot online terpercaya: situs judi online resmi Indonesia – situs judi online resmi Indonesia
AaronJet
Starburst giri gratis senza deposito giocare a Starburst gratis senza registrazione giocare a Starburst gratis senza registrazione
Jamespug
http://www.stroyexpertsochi.ru Ознакомьтесь с наши проекты и ознакомьтесь с передовыми технологиями террасирования и укрепления склонов.
Miltonlef
agen garuda888 bonus new member: agen garuda888 bonus new member – daftar garuda888 mudah dan cepat
pansimskelusa
пансионат для пожилых
pansionat-msk008.ru
пансионаты для инвалидов в москве
pansionattulaelusa
пансионат для реабилитации после инсульта
pansionat-tula008.ru
частный дом престарелых
AlfredJag
https://1win69.shop/# preman69 login tanpa ribet
Jamespug
stroyexpertsochi.ru/ Изучите портфолио объектов и ознакомьтесь с безопасными и комфортными решениями для семьи.
internetfrofs
провайдеры по адресу дома
inernetvkvartiru-ekaterinburg005.ru
подключить интернет в екатеринбурге в квартире
Jamespug
геопластика участка сочи Выбирайте геопластику участка в Сочи и обеспечьте стабильность вашего дома.
StevenTaf
http://truemedspharm.com/# TrueMeds
Jamespug
защита стен от грибка Сочи Применяйте защиту стен от грибка Сочи и обеспечьте безопасность стен.
pansitulaelusa
частные пансионаты для пожилых в туле
pansionat-tula009.ru
частный пансионат для пожилых людей
domprestarelihmskelusa
пансионат для лежачих пожилых
pansionat-msk009.ru
пансионат для пожилых
Frankjuink
capsule online pharmacy: american online pharmacy – peoples pharmacy
Jamespug
stroyexpertsochi.ru/ Проверяйте портфолио объектов и ознакомьтесь с ландшафтным дизайном и террасированием участков.
Michaelbar
TrueMeds Pharmacy: bitcoin pharmacy online – legitimate mexican pharmacy online
Antoniopierb
canadian pharmacy service TrueMeds Pharmacy viagra online canadian pharmacy
internetfrofs
домашний интернет в екатеринбурге
inernetvkvartiru-ekaterinburg006.ru
подключение интернета екатеринбург
Jamespug
http://stroyexpertsochi.ru Просмотрите наш каталог решений и получите рекомендации по благоустройству участка с уклоном и укреплению склона.
Jamespug
http://stroyexpertsochi.ru Посетите наш каталог решений и узнайте о теплоизоляции, энергоэффективных окнах и дверях.
Jamespug
https://stroyexpertsochi.ru/ Просмотрите наш сайт и изучите практические рекомендации по строительству, отделке и благоустройству домов.
StevenTaf
http://truemedspharm.com/# canadian pharmacy no rx needed
DanielGopay
https://vitalcorepharm.com/# VitalCore
Jamespug
https://www.stroyexpertsochi.ru Загляните на материалы и изучите возможности современного ландшафтного дизайна и террасирования.
Frankjuink
online ed pharmacy: pills for erectile dysfunction online – VitalCore Pharmacy
Michaelbar
vipps canadian pharmacy: TrueMeds – TrueMeds Pharmacy
Jamespug
stroyexpertsochi.ru Просмотрите наши материалы и узнайте о материалах, идеально подходящих для морского и влажного климата.
Antoniopierb
online pharmacy delivery delhi foreign pharmacy online TrueMeds
Jamespug
http://stroyexpertsochi.ru Погрузитесь в наш каталог решений и узнайте о безопасных и комфортных решениях для вашей семьи).
inernetadresfrofs
провайдеры интернета по адресу красноярск
inernetvkvartiru-krasnoyarsk004.ru
узнать интернет по адресу
Jamespug
stroyexpertsochi.ru Проверьте наши материалы и получите максимум информации о фундаменте, бетонных и монолитных конструкциях.
Jamespug
https://stroyexpertsochi.ru/ Откройте наш сайт и получите рекомендации по строительству и ремонту домов в Сочи.
Michaelbar
best canadian pharmacy for viagra: TrueMeds Pharmacy – TrueMeds Pharmacy
Frankjuink
VitalCore Pharmacy: VitalCore Pharmacy – ed pills
Jamespug
stroyexpertsochi.ru Просмотрите наши материалы и узнайте о материалах, идеально подходящих для морского и влажного климата.
StevenTaf
http://clearmedspharm.com/# buy antibiotics
Antoniopierb
buy antibiotics online cheap antibiotics buy antibiotics for tooth infection
lecheniemskelusa
психиатрическая помощь на дому
psychiatr-moskva005.ru
консультация врача психиатра
Jamespug
https://www.stroyexpertsochi.ru/ Посетите раздел “Отзывы клиентов” и узнайте о защите стен от грибка и антикоррозийной обработке металлоконструкций.
pansionattulaelusa
частные пансионаты для пожилых в туле
pansionat-tula008.ru
пансионат для пожилых в туле
inernetadresfrofs
проверить интернет по адресу
inernetvkvartiru-krasnoyarsk005.ru
провайдер интернета по адресу красноярск
Jamespug
https://www.stroyexpertsochi.ru Изучите материалы и изучите современные методы теплоизоляции и энергоэффективных окон.
DanielGopay
http://truemedspharm.com/# TrueMeds
Jamespug
благоустройство участка с уклоном Применяйте благоустройство участка с уклоном и обустраивайте удобный ландшафт.
Michaelbar
canada discount pharmacy: TrueMeds – online med pharmacy
Jamespug
https://stroyexpertsochi.ru Просмотрите галерею выполненных работ и ознакомьтесь с технологиями благоустройства территории и проектирования дома.
psikhiatrmskelusa
лечение в психиатрической больнице
psychiatr-moskva006.ru
вызвать психиатра на дом
Frankjuink
24 hr pharmacy: online pharmacy without prescription – TrueMeds Pharmacy
StevenTaf
https://truemedspharm.com/# TrueMeds Pharmacy
Jamespug
http://www.stroyexpertsochi.ru Проверяйте наши проекты и узнайте обо всех тонкостях фундамента, дренажных систем и сейсмоустойчивых технологий.
Antoniopierb
antibiotics over the counter ClearMeds Pharmacy
pansionattulaelusa
частный дом престарелых
pansionat-tula009.ru
пансионат после инсульта
inernetadresfrofs
интернет провайдеры по адресу
inernetvkvartiru-krasnoyarsk006.ru
какие провайдеры по адресу
Jamespug
водостойкая штукатурка Сочи Используйте водостойкую штукатурку в Сочи и обеспечьте защиту ваших объектов.
Jamespug
stroyexpertsochi.ru/ Исследуйте портфолио объектов и получите рекомендации по строительству коттеджей и домов под ключ.
Jamespug
https://www.stroyexpertsochi.ru/ Ознакомьтесь с раздел “Отзывы клиентов” и получите практические советы по проектированию, укреплению склона и благоустройству участка.
Michaelbar
buy antibiotics online safely: ClearMeds Pharmacy –
Kennithraw
материалы для морского климата Используйте надежные материалы для морского климата и гарантируйте себе в сохранности вашего здания.
Frankjuink
ClearMeds: buy antibiotics – buy antibiotics online safely
StevenTaf
https://vitalcorepharm.com/# VitalCore Pharmacy
Kennithraw
http://www.stroyexpertsochi.ru Узнайте больше на наши проекты и ознакомьтесь с передовыми подходами к проектированию коттеджей и частных домов.
Antoniopierb
erectile dysfunction medicine online VitalCore VitalCore
Kennithraw
http://stroyexpertsochi.ru/ Исследуйте раздел услуг и получите практические советы по строительству частного дома под ключ и отделке коттеджей.
psihiatrmskelusa
нужна консультация психиатра
psikhiatr-moskva004.ru
психиатрическая помощь госпитализация
Kennithraw
stroyexpertsochi.ru/ Просмотрите портфолио объектов и получите советы по благоустройству участка с уклоном и геопластике.
psihmskelusa
частная психиатрическая клиника стационар
psychiatr-moskva004.ru
вызов психиатра на дом в москве
inernetkrdfrofs
провайдеры в краснодаре по адресу проверить
inernetvkvartiru-krasnodar004.ru
провайдеры в краснодаре по адресу проверить
DanielGopay
https://vitalcorepharm.com/# VitalCore
Kennithraw
http://stroyexpertsochi.ru/ Зайдите на раздел услуг и получите советы по выбору материалов для морского и влажного климата.
Michaelbar
VitalCore: erectile dysfunction online prescription – VitalCore
Kennithraw
https://stroyexpertsochi.ru/ Исследуйте наш сайт и получите советы по энергоэффективным коттеджам и установке солнечных панелей.
Malikanold
kamagra gel oral livraison discrète France: kamagra gel oral livraison discrète France – kamagra gel oral livraison discrète France
psihmskelusa
консультация психиатра круглосуточно
psikhiatr-moskva005.ru
принудительное психиатрическое лечение
KennethFug
sildenafil citrate 100 mg livraison rapide et confidentielle sildenafil citrate 100 mg
Kennithraw
http://www.stroyexpertsochi.ru Ознакомьтесь с наш сайт и получите информацию о геопластике участка и оптимальном использовании пространства.
lecheniemskelusa
психиатрическая помощь
psychiatr-moskva005.ru
консультация психиатра платно
WilliamWhike
https://bluepharmafrance.shop/# viagra femme
inernetkrdfrofs
подключение интернета по адресу
inernetvkvartiru-krasnodar005.ru
провайдеры интернета по адресу
AnthonyRam
PharmaLibre: kamagra 100 mg prix competitif en ligne – kamagra
Malikanold
cialis sans ordonnance: IntimaPharma France – tadalafil prix
psihiatrmskelusa
психиатрическая клиника
psikhiatr-moskva006.ru
платный психиатр на дом в москве
KennethFug
pharmacie en ligne france commander medicaments livraison rapide vente de mГ©dicament en ligne
inernetkrdfrofs
подключить интернет по адресу
inernetvkvartiru-krasnodar006.ru
проверить провайдеров по адресу краснодар
psychiatrmskelusa
платная психиатрическая клиника
psychiatr-moskva006.ru
частный психиатрический стационар
WilliamWinue
https://pharmaexpressfrance.com/# pharmacie en ligne pas cher
AnthonyRam
tadalafil 20 mg en ligne: acheter mГ©dicament en ligne sans ordonnance – IntimaPharma France
izzapoyaastanaelusa
курс реабилитации наркозависимых в Астане
reabilitaciya-astana004.ru
реабилитация алкоголиков цены в Астане
Malikanold
kamagra: PharmaLibre France – PharmaLibre France
KennethFug
commander cialis discretement medicament contre la dysfonction erectile tadalafil prix
internetfrofs
узнать провайдера по адресу москва
inernetvkvartiru-msk004.ru
интернет по адресу москва
psikhiatrmskelusa
платная психиатрическая скорая помощь
psikhiatr-moskva004.ru
врач психиатр на дом
AnthonyRam
viagra femme: BluePharma France – BluePharma
zapojastanaelusa
реабилитация зависимых от алкоголя в Астане
reabilitaciya-astana005.ru
реабилитация от наркозависимости
internetfrofs
проверить провайдера по адресу
inernetvkvartiru-msk005.ru
домашний интернет
psihiatrmskelusa
платный психиатр на дом
psikhiatr-moskva005.ru
лечение в психиатрическом стационаре
KennethFug
medicaments generiques et originaux France pharmacie en ligne sans ordonnance pharmacie en ligne france fiable
WilliamWinue
https://pharmaexpressfrance.com/# Pharmacie sans ordonnance
zapojastanaelusa
реабилитация наркозависимых
reabilitaciya-astana006.ru
анонимное лечение от алкоголизма
WilliamWhike
http://pharmalibrefrance.com/# PharmaLibre
AnthonyRam
PharmaLibre France: acheter kamagra pas cher livraison rapide – kamagra gel oral livraison discrete France
internetfrofs
интернет домашний москва
inernetvkvartiru-msk006.ru
какие провайдеры по адресу
FobertLautt
An impressive share! I’ve just forwarded this onto a co-worker who had been doing a little research on this. And he actually bought me dinner because I stumbled upon it for him… lol. So allow me to reword this…. Thanks for the meal!! But yeah, thanks for spending some time to discuss this topic here on your website.
kidsvisitor
psihmskelusa
лечение в психиатрическом стационаре
psikhiatr-moskva006.ru
стационар психиатрической больницы
KennethFug
viagra en ligne France sans ordonnance Viagra homme prix en pharmacie sans ordonnance viagra femme
izzapoyatulaelusa
экстренный вывод из запоя тула
tula-narkolog004.ru
лечение запоя
AnthonyRam
pilule bleue en ligne: Prix du Viagra 100mg en France – BluePharma France
WilliamWhike
https://intimapharmafrance.shop/# cialis generique pas cher
internetfrofs
домашний интернет подключить нижний новгород
inernetvkvartiru-nizhnij-novgorod004.ru
провайдер по адресу
narkologiyaastanaelusa
лечение наркомании
reabilitaciya-astana004.ru
отправить на лечение наркомана
lechenietulaelusa
экстренный вывод из запоя тула
tula-narkolog005.ru
лечение запоя тула
KennethFug
PharmaExpress France pharmacie en ligne pas cher pharmacie en ligne france livraison internationale
WilliamWinue
https://bluepharmafrance.shop/# livraison rapide et confidentielle
internetfrofs
какие провайдеры интернета есть по адресу нижний новгород
inernetvkvartiru-nizhnij-novgorod005.ru
домашний интернет тарифы нижний новгород
AnthonyRam
acheter medicaments en ligne pas cher: pharmacie digitale francaise fiable – pharmacie en ligne france livraison internationale
zapojastanaelusa
реабилитация наркоманов в Астане
reabilitaciya-astana005.ru
реабилитация наркозависимых стационар
JerryVak
https://bluepharmafrance.shop/# viagra générique efficace
lechenietulaelusa
вывод из запоя
tula-narkolog006.ru
лечение запоя тула
internetfrofs
домашний интернет нижний новгород
inernetvkvartiru-nizhnij-novgorod006.ru
домашний интернет подключить нижний новгород
Josephquiff
https://linklist.bio/kratonbet777# kratonbet alternatif
izzapoyachelyabinskelusa
вывод из запоя цена
vivod-iz-zapoya-chelyabinsk007.ru
вывод из запоя круглосуточно челябинск
vivodzapojastanaelusa
лечение от алкогольной зависимости
reabilitaciya-astana006.ru
лечение алкоголизма цены
Charlesirrep
betawi77 login betawi77 net betawi 77 slot
Stevensew
bataraslot alternatif: batara88 – bataraslot 88
internetfrofs
провайдеры интернета новосибирск
inernetvkvartiru-novosibirsk004.ru
подключить интернет в квартиру новосибирск
Arnette
united states no deposit pokies, best online pokies united kingdom forum and
legit australian online friday casino Bonus codes, or betsoft no deposit bonus united states
narkologiyachelyabinskelusa
вывод из запоя цена
vivod-iz-zapoya-chelyabinsk008.ru
экстренный вывод из запоя челябинск
alkogolizmtulaelusa
вывод из запоя круглосуточно
tula-narkolog004.ru
экстренный вывод из запоя
Charlesirrep
Login Alternatif Togel INA TOGEL Daftar Situs Togel Toto 4D
Stevensew
betawi 777: betawi 77 – betawi 77 slot
Josephquiff
https://linktr.ee/bataraslot777# bataraslot 88
internetfrofs
подключить интернет в квартиру новосибирск
inernetvkvartiru-novosibirsk005.ru
домашний интернет в новосибирске
zapojchelyabinskelusa
лечение запоя
vivod-iz-zapoya-chelyabinsk009.ru
лечение запоя
vivodzapojtulaelusa
вывод из запоя цена
tula-narkolog005.ru
вывод из запоя тула
Charlesirrep
toto slot hargatoto toto slot hargatoto hargatoto login
Stevensew
betawi 77: betawi 777 – betawi77 login
vivodcherepovecelusa
вывод из запоя цена
vivod-iz-zapoya-cherepovec010.ru
вывод из запоя круглосуточно череповец
internetfrofs
провайдеры по адресу дома
inernetvkvartiru-novosibirsk006.ru
узнать интернет по адресу
blazecrew2Itamy
Je suis accro a DBosses, ca donne un frisson inegale. La gamme est tout simplement epoustouflante, incluant des jeux de table sophistiques. Le service client est d’une classe exceptionnelle, avec une aide personnalisee. Les retraits sont fluides et ultra-rapides, cependant plus de tours gratuits seraient top. En fin de compte, DBosses est une plateforme hors norme pour les fans de jeux modernes ! Notons aussi le site est style et bien concu, facilite une immersion totale.
dbosses casino bonus|
zestycrow4Itamy
Je suis accro a Celsius Casino, ca degage une ambiance de jeu torride. Le repertoire du casino est une veritable fournaise de divertissement, comprenant des jeux de casino optimises pour les cryptomonnaies. L’assistance du casino est chaleureuse et efficace, repondant en un eclair ardent. Le processus du casino est transparent et sans combustion, par moments des bonus de casino plus frequents seraient torrides. Globalement, Celsius Casino est une pepite pour les fans de casino pour les explorateurs du casino ! En plus l’interface du casino est fluide et eclatante comme une flamme, donne envie de replonger dans le casino a l’infini.
celsius casino 50 free spins|
vivodzapojtulaelusa
вывод из запоя тула
tula-narkolog006.ru
вывод из запоя тула
fuzzypanda7Itamy
J’adore le delire total de Gamdom, on dirait une explosion de fun. Le catalogue de jeux est juste enorme, proposant des sessions live qui tabassent. Le support est dispo 24/7, offrant des reponses qui petent. Les gains arrivent en mode TGV, mais bon des bonus plus reguliers ce serait la classe. Pour resumer, Gamdom c’est du lourd a tester direct pour ceux qui kiffent parier avec style ! Bonus l’interface est fluide et stylee a mort, booste l’immersion a fond les ballons.
gamdom condition withdraw|
Thomascrurn
https://linkr.bio/betawi777# betawi 77
alkogolizmcherepovecelusa
экстренный вывод из запоя череповец
vivod-iz-zapoya-cherepovec011.ru
вывод из запоя
Josephquiff
https://linklist.bio/inatogelbrand# Official Link Situs Toto Togel
Stevensew
betawi 77 slot: betawi77 – betawi 77
Charlesirrep
batara88 slot online batara88
internetrostovfrofs
домашний интернет
inernetvkvartiru-rostov004.ru
провайдеры интернета ростов
zapojchelyabinskelusa
вывод из запоя цена
vivod-iz-zapoya-chelyabinsk007.ru
лечение запоя челябинск
alkogolizmcherepovecelusa
вывод из запоя цена
vivod-iz-zapoya-cherepovec012.ru
вывод из запоя круглосуточно
thunderwave8Itamy
Je suis fascine par Circus, il propose un spectacle ludique unique. Il y a une profusion de titres captivants, incluant des jeux de table dynamiques. Le support est disponible 24/7, offrant des solutions claires et rapides. Les gains arrivent sans attendre, de temps a autre plus de tours gratuits seraient un atout. En fin de compte, Circus vaut pleinement le detour pour les fans de jeux modernes ! Par ailleurs la plateforme est visuellement impressionnante, ajoute une touche de magie.
circus circus casino reno nevada|
wildpickle3Itamy
Je suis accro au style de FatPirate, ca balance une vibe dechainee. Il y a un ocean de titres varies, offrant des machines a sous qui claquent. Le support est dispo 24/7, joignable par chat ou email. Les retraits sont rapides comme une tempete, par moments des recompenses en plus ca serait la cerise. Pour resumer, FatPirate garantit un fun total pour les accros aux sensations fortes ! A noter aussi la plateforme claque avec son look unique, booste l’immersion a fond.
fatpirate casino review|
flickergoose3Itamy
Je suis accro a Amon Casino, il offre une experience de casino electrisante. La selection de titres du casino est juste insensee, comprenant des jeux de casino adaptes aux cryptomonnaies. Le staff du casino assure un suivi de ouf, offrant des solutions claires et instantanees. Les gains du casino arrivent a la vitesse de l’eclair, quand meme j’aimerais plus de promos de casino qui tabassent. En bref, Amon Casino offre une experience de casino inoubliable pour les accros aux sensations fortes du casino ! En bonus la navigation du casino est simple comme un claquement de doigts, ajoute un max de swag au casino.
amon casino france|
Stevensew
kratonbet login: kratonbet link – kratonbet
quirkytoad9Itamy
Je suis scotche par Impressario, on dirait une scene de fun explosif. Les options sont variees et eblouissantes, offrant des machines a sous qui claquent. L’assistance est une vraie performance de pro, offrant des reponses qui scintillent. Le processus est limpide et sans fausse note, de temps en temps j’aimerais plus de promos qui envoutent. Au final, Impressario offre un spectacle de jeu inoubliable pour les amateurs de slots qui brillent ! Cote plus le design est une explosion visuelle, booste l’immersion a fond.
impressario casino|
internetrostovfrofs
домашний интернет тарифы
inernetvkvartiru-rostov005.ru
интернет провайдер ростов
Charlesirrep
INA TOGEL Daftar INA TOGEL Daftar inatogel 4D
vivodchelyabinskelusa
вывод из запоя круглосуточно
vivod-iz-zapoya-chelyabinsk008.ru
лечение запоя
zapojirkutskelusa
экстренный вывод из запоя иркутск
vivod-iz-zapoya-irkutsk007.ru
экстренный вывод из запоя
internetrostovfrofs
домашний интернет подключить ростов
inernetvkvartiru-rostov006.ru
домашний интернет тарифы
Stevensew
batarabet alternatif: batarabet – batarabet login
Charlesirrep
mawartoto alternatif mawartoto link mawartoto link
starblaze6Itamy
Je trouve incroyable Cresus, on ressent une energie magique. Le catalogue est d’une richesse eblouissante, avec des slots modernes et immersifs. Le service client est royal, offrant des solutions claires et rapides. Les retraits sont fluides et rapides, cependant plus de tours gratuits seraient un plus. Dans l’ensemble, Cresus garantit un divertissement princier pour ceux qui aiment parier avec elegance ! En plus la navigation est intuitive et rapide, ce qui rend chaque session encore plus memorable.
casino cresus gratuit|
moonbadger7Itamy
Ich bin suchtig nach DrueGlueck Casino, es bietet eine krasse Spielerfahrung. Die Spielauswahl im Casino ist gigantisch, mit modernen Casino-Slots, die fesseln. Die Casino-Mitarbeiter sind blitzschnell und top, mit Hilfe, die richtig abgeht. Auszahlungen im Casino sind blitzschnell, trotzdem die Casino-Angebote konnten gro?zugiger sein. Zusammengefasst ist DrueGlueck Casino ein Casino mit mega Spielspa? fur die, die mit Stil im Casino wetten! Extra die Casino-Oberflache ist flussig und mega cool, was jede Casino-Session noch krasser macht.
drueckglueck live casino review|
GichardTes
Wow, marvelous blog layout! How lengthy have you ever been blogging for? you made blogging look easy. The whole glance of your site is wonderful, as neatly as the content!
сайт кракен
izzapoyachelyabinskelusa
вывод из запоя круглосуточно
vivod-iz-zapoya-chelyabinsk009.ru
вывод из запоя круглосуточно челябинск
twistyprawn8Itamy
Je suis accro a AmunRa Casino, ca balance une vibe de jeu pharaonique. Le catalogue de jeux du casino est colossal, avec des machines a sous de casino modernes et immersives. Le support du casino est dispo 24/7, garantissant un support de casino instantane et royal. Les paiements du casino sont securises et fiables, de temps en temps j’aimerais plus de promos de casino qui eblouissent. En bref, AmunRa Casino est un casino en ligne qui regne en maitre pour les fans de casinos en ligne ! De surcroit la plateforme du casino brille avec un look de legende, ce qui rend chaque session de casino encore plus envoutante.
amunra aplikacja|
alkogolizmirkutskelusa
экстренный вывод из запоя
vivod-iz-zapoya-irkutsk008.ru
лечение запоя
Thomascrurn
https://tap.bio/@hargatoto# hargatoto login
cosmicgecko1Itamy
Je kiffe grave Instant Casino, il propose une experience de casino explosive. La gamme de casino est un veritable feu d’artifice, proposant des sessions de casino live qui dechirent. Les agents du casino sont rapides comme l’eclair, repondant en un flash. Les paiements du casino sont fluides et securises, par contre des recompenses de casino en plus ca ferait kiffer. Dans le fond, Instant Casino c’est un casino de ouf a tester direct pour les pirates des slots de casino modernes ! Cote plus le site du casino est une tuerie graphique, facilite le delire total au casino.
aladdins gold casino instant play|
internetfrofs
подключить домашний интернет санкт-петербург
inernetvkvartiru-spb004.ru
домашний интернет тарифы
Stevensew
Login Alternatif Togel: Daftar InaTogel Login Link Alternatif Terbaru – INA TOGEL Daftar
Charlesirrep
batara vip batarabet alternatif batara88
alkogolizmirkutskelusa
лечение запоя
vivod-iz-zapoya-irkutsk009.ru
экстренный вывод из запоя
zapojcherepovecelusa
вывод из запоя череповец
vivod-iz-zapoya-cherepovec010.ru
вывод из запоя круглосуточно
sparklemoth8Itamy
Achou loucamente incrivel DazardBet Casino, oferece uma experiencia de cassino que e fogo puro. A gama do cassino e simplesmente um espetaculo, com caca-niqueis de cassino modernos e imersivos. O servico do cassino e top e confiavel, respondendo num piscar de olhos. O processo do cassino e limpo e sem complicacao, mesmo assim as ofertas do cassino podiam ser mais generosas. Resumindo, DazardBet Casino e o point perfeito pros fas de cassino para os aventureiros do cassino! De bonus a plataforma do cassino arrasa com um visual eletrizante, o que deixa cada sessao de cassino ainda mais insana.
dazardbet bonus|
fluffycactus3Itamy
Je trouve absolument epique Julius Casino, il propose une aventure de casino digne d’un empereur. La collection de jeux du casino est colossale, incluant des jeux de table de casino d’une noblesse rare. Le personnel du casino offre un accompagnement imperial, repondant en un eclair de glaive. Les gains du casino arrivent a une vitesse triomphale, parfois les offres du casino pourraient etre plus genereuses. En somme, Julius Casino promet un divertissement de casino heroique pour les joueurs qui aiment parier avec panache au casino ! Par ailleurs la navigation du casino est intuitive comme une strategie romaine, amplifie l’immersion totale dans le casino.
julius casino site officiel|
spunkyfrog2Itamy
Je suis dingue de Bruno Casino, il propose une aventure de casino pleine de panache. La collection de jeux du casino est phenomenale, proposant des slots de casino a theme audacieux. Les agents du casino sont vifs comme l’eclair, joignable par chat ou email. Les retraits au casino sont rapides comme une fusee, mais des recompenses de casino supplementaires feraient vibrer. Pour resumer, Bruno Casino est un casino en ligne qui fait des vagues pour ceux qui cherchent l’adrenaline du casino ! Bonus le site du casino est une merveille graphique, amplifie l’immersion totale dans le casino.
casino val andre – partouche|
fluffycrab3Itamy
Acho simplesmente animal LeaoWin Casino, da uma energia de cassino que e indomavel. Tem uma enxurrada de jogos de cassino irados, oferecendo sessoes de cassino ao vivo que sao um rugido. O suporte do cassino ta sempre na area 24/7, dando solucoes na hora e com precisao. Os ganhos do cassino chegam voando como uma aguia, mas mais giros gratis no cassino seria uma loucura. Resumindo, LeaoWin Casino vale demais explorar esse cassino para quem curte apostar com garra no cassino! De bonus o design do cassino e uma explosao visual feroz, aumenta a imersao no cassino a mil.
leaowin02 casino ??????|
internetfrofs
провайдеры по адресу
inernetvkvartiru-spb005.ru
проверить провайдера по адресу
Charlesirrep
kratonbet link kratonbet kratonbet alternatif
vivodzapojkalugaelusa
вывод из запоя цена
vivod-iz-zapoya-kaluga010.ru
вывод из запоя круглосуточно калуга
Stevensew
betawi 77: betawi 77 – betawi 77 slot
vivodzapojcherepovecelusa
лечение запоя череповец
vivod-iz-zapoya-cherepovec011.ru
вывод из запоя круглосуточно череповец
alkogolizmkalugaelusa
лечение запоя калуга
vivod-iz-zapoya-kaluga011.ru
экстренный вывод из запоя калуга
internetfrofs
провайдеры по адресу санкт-петербург
inernetvkvartiru-spb006.ru
узнать провайдера по адресу санкт-петербург
Charlesirrep
bataraslot batarabet alternatif batarabet