Outsourcing electronic manufacturing can save businesses time, reduce costs, and help achieve better scalability. However, when creating a new project, it’s important to approach outsourcing tasks with care to avoid costly mistakes. Poor planning or choosing the wrong outsourcing partner can lead to design flaws, production delays, and increased expenses. This blog highlights 6 common mistakes to avoid when outsourcing electronic manufacturing and offers practical advice for a smooth and successful experience.
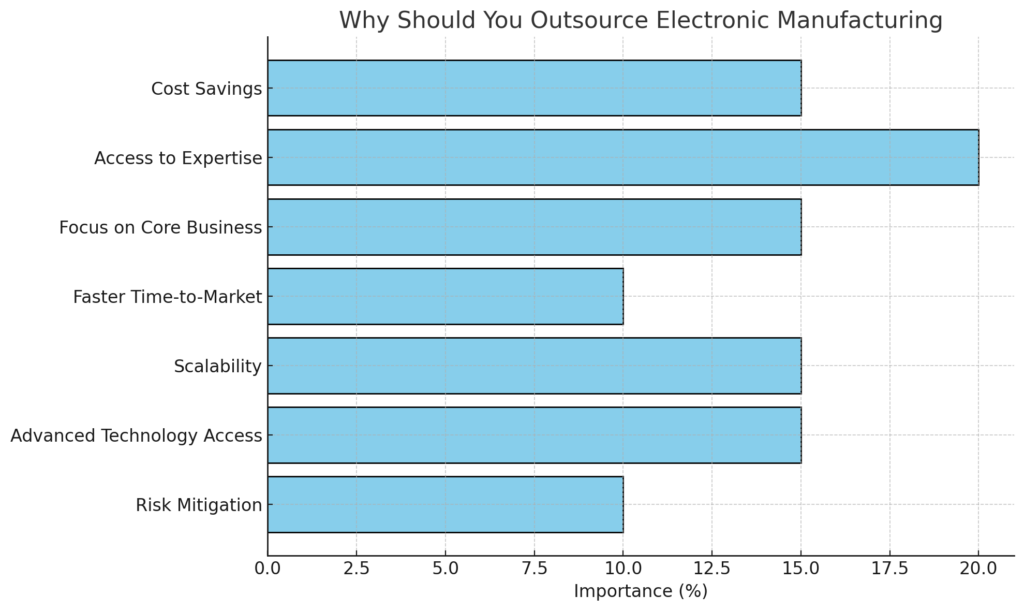
1. Failing to Define Clear Project Requirements
One of the biggest mistakes businesses make when outsourcing an assembly or other manufacturing tasks is failing to clearly outline their requirements. Without detailed project guidelines, manufacturers may produce components that fail to meet expectations.
Why It’s a Mistake?
- It increases the risk of miscommunication and errors.
- Leads to unnecessary delays and added costs.
How to Avoid?
- Draft a detailed project plan when creating a new project.
- Specify technical requirements, timelines, and quality expectations.
- Collaborate with your outsourcing partner to confirm that they fully understand the scope.
This step is essential to ensure that you avoid design and production errors that could affect the final product’s quality.
2. Selecting the Wrong Manufacturer
Choosing an inexperienced or unsuitable outsourcing partner is another common mistake. Not all manufacturers have the resources or expertise to handle specific projects, leading to subpar results.
Why It’s a Mistake?
- It could compromise product quality.
- You may encounter delays or budget overruns.
How to Avoid?
- Research potential manufacturers thoroughly.
- Look for certifications like ISO 9001 or industry-specific qualifications.
- Evaluate their past work and client testimonials.
However, remember, a good manufacturer will feel like an extension of your own team. For example, Cygnus Electronics specializes in electronic manufacturing services and offers expertise in design, development, and turnkey solutions tailored to your business needs. So, if you’re looking for a trusted partner, reach out to Cygnus for a consultation today!
3. Overlooking Communication Processes
Effective communication is vital when outsourcing tasks, especially in complex projects like electronics manufacturing. A lack of structured communication can lead to misunderstandings and prevent issues from being resolved promptly.
Moreover, open communication ensures you’re aligned with your manufacturer and reduces the risk of design and production errors.
Why It’s a Mistake?
- Updates may be missed, causing delays.
- Problems may escalate if not addressed early.
How to Avoid?
- Set up regular check-ins with your outsourcing partner.
- Use project management tools to track progress and address issues in real time.
- Ensure both teams have designated contacts for better coordination.
4. Ignoring Quality Control Measures
Many businesses assume that manufacturers will automatically uphold high-quality standards. However, neglecting quality checks throughout the process can result in defective products that are expensive to fix later.
Pro tip: Always include quality checks at every stage of the production process. Ask your manufacturer:
- Do they follow industry standards (like ISO certifications)?
- What are their testing capabilities?
- How do they handle defects?
Why It’s a Mistake?
- Quality issues can harm your brand reputation.
- Fixing defects post-production can delay project delivery.
How to Avoid?
- Implement a robust quality control system when outsourcing an assembly.
- Inspect samples and prototypes before full-scale production begins.
- Partner with a manufacturer with a proven track record of quality assurance.
5. Neglecting to Protect Your Designs and Ideas
Your intellectual property (IP) represents the heart of your innovation and creativity. It’s not just a collection of designs or concepts, it’s what differentiates your business in a competitive market. Neglecting to protect these valuable assets when outsourcing electronic manufacturing can result in devastating consequences, including unauthorized use, loss of competitive edge, and even theft.
When you share your designs and concepts with a third-party manufacturer, you’re essentially placing your trust in their ability to respect and safeguard your IP. Without proper measures in place, you risk losing control over your hard-earned ideas.
Why It’s a Mistake?
- Competitors could access your designs.
- It may affect your competitive edge in the market.
How to Avoid?
- Sign non-disclosure agreements (NDAs) with your outsourcing partner.
- Include IP protection clauses in your contracts.
- Collaborate with manufacturers in regions with strong IP laws.
Also Read: How to choose the best material for PCB
6. Focusing Solely on Cost
Any company choice is usually heavily influenced by cost, and outsourcing electrical production is no exception. But even while it would be tempting to go with the least expensive choice, doing so can result in long-term problems and more expenses later on.
You’re missing out on other important factors like quality, dependability, and the whole value a manufacturer can add to your project when you only consider pricing.
Why It’s a Mistake?
- Poor-quality components can harm your brand.
- You might face increased costs in the long run to correct errors.
How to Avoid?
- Evaluate the manufacturer’s reliability, quality standards, and scalability in addition to cost.
- Opt for a manufacturer offering a balance between affordability and high standards.
- Focus on long-term value instead of short-term savings.
Click here to find out how you can reduce PCB design cost
Final Thoughts
Outsourcing electronic manufacturing is a strategic decision that can deliver significant benefits, but it also comes with challenges. However, avoiding common pitfalls, like unclear requirements, poor communication, or ignoring quality control can make the process smoother and more efficient.
When you’re going to create a new project, it’s important to choose the right outsourcing partner like Cygnus Corp and ensure effective collaboration. This will help you avoid design and production errors while staying within budget and on schedule.