Do you wanna know the benefits of lean manufacturing in EMS? lean manufacturing is a simple yet powerful way of working that focuses on reducing waste, improving processes, and delivering more value to customers. For companies in Electronic Manufacturing Services (EMS), lean manufacturing can be a real game-changer.
Take out a moment and suppose you’re running an EMS business, handling complex orders, tight deadlines, and customers who expect nothing but the best. Every mistake, delay, or extra cost can hurt your business. Lean manufacturing helps you fix these issues by making your operations smooth, flexible, and focused on what matters most.
Either you’re making parts for the latest smartphones or electronics for electric vehicles, lean manufacturing helps you produce better quality products faster and at a lower cost. But what exactly is lean manufacturing? And how can it make a difference for EMS businesses like yours?
In this blog, we’ll explain how lean manufacturing works as well as discuss the benefits of lean manufacturing in EMS.
Also Read: Electronic manufacturing for small scale businesses.
What is Lean Manufacturing in EMS?
Lean manufacturing is a production methodology designed to eliminate waste, streamline workflows, and deliver high-quality products efficiently. In the EMS industry, the lean manufacturing process focuses on optimizing resources, improving quality, and meeting customer demands faster and more effectively.
The benefits of lean manufacturing in EMS are substantial. When EMS providers use lean manufacturing techniques, they can boost productivity, improve quality, and shorten lead times and ensure they remain competitive in a fast-evolving market. These techniques help businesses focus on continuous improvement, value addition, and waste reduction across all operations.
Click here to read out the smart strategies you can use to minimize manufacturing cost
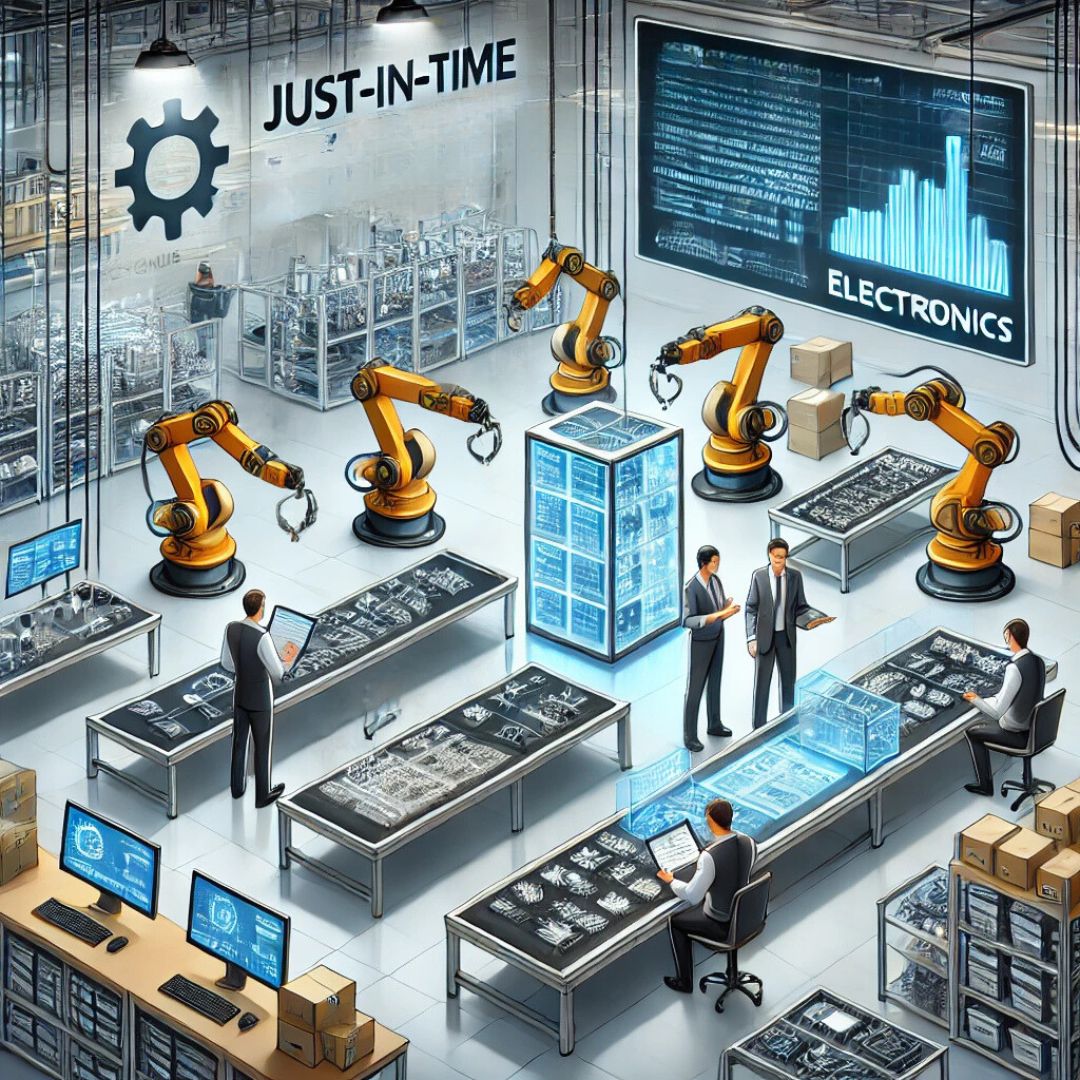
Benefits of Lean Manufacturing in EMS
1. Boosts Efficiency and Reduces Waste
The primary goal of lean manufacturing in EMS is to identify and eliminate waste whether it’s wasted materials, time, or labor. Manufacturers can streamline processes, reduce costs, and deliver products faster by focusing on efficient workflows. For example, lean practices like just-in-time (JIT) inventory management ensure materials are used when needed to avoid overproduction and storage costs.
2. Improves Quality Control
Quality is an important consideration in lean manufacturing strategies at all stages of production. EMS providers may reduce problems and maintain consistent product delivery by implementing strategies such as continuous monitoring and error proofing. This emphasis on quality not only increases consumer trust, but it also lowers the costs of rework and recall.
3. Enhances Productivity and Competitiveness
When companies implement the lean manufacturing process it helps them to optimize resources and focus on value-adding activities. With better workflows and reduced inefficiencies, EMS providers can increase output without increasing costs. As a result, they improve performance and competitiveness, standing out in a crowded market.
4. Shortens Lead Time
In the electronics sector, where consumer needs may change rapidly, speed is essential. However, lean manufacturing in EMS guarantees faster production cycles by removing bottlenecks and optimizing processes. In the end, this enables EMS providers to deliver goods to clients more quickly by achieving gains in productivity, quality, and lead time.
5. Eco-Friendly Practices
Waste reduction in lean manufacturing isn’t just about cutting costs, it also aligns with environmental sustainability. EMS companies practicing lean can reduce energy consumption, lower material waste, and contribute to greener manufacturing practices.
- Fact: Studies show that adopting lean methods can decrease industrial waste by up to 25%, a significant win for the environment.
6. Ecourages Employee Engagement
An effective lean daily management system guarantees that staff members actively participate in decision-making and problem-solving. In the end, this raises morale and productivity by fostering a sense of accountability and ownership. Workers are more driven to produce excellent work when they are aware of and supportive of the organization’s lean objectives.
Challenges in Adopting Lean Manufacturing in EMS
While the benefits are clear, adopting lean manufacturing in the EMS sector isn’t without its challenges.
1. Complex Supply Chains
EMS companies often work with global suppliers. Using lean manufacturing means carefully planning and coordinating to make sure parts arrive on time.
2. High Initial Investment
Transitioning to lean manufacturing may involve upfront costs for training, equipment upgrades, or system reorganization.
3. Cultural Shift
Lean manufacturing demands a culture of continuous improvement. Employees must be encouraged to identify inefficiencies and suggest improvements, a mindset shift for many traditional workplaces.
4. Demand Volatility
The electronics industry is highly unpredictable. Therefore, balancing lean inventory practices with fluctuating customer demands requires careful planning and agility.
5. Ongoing Commitment:
Lean manufacturing is not a one-time effort, it requires continuous monitoring and improvement.
How Cygnus Electronics Implements Lean Manufacturing
Lean manufacturing isn’t simply a catchphrase at Cygnus Electronics; it’s the foundation of everything we do. We use lean concepts to provide outstanding outcomes, from optimized design and development procedures to effective procurement and turnkey solutions.
Our dedication to reducing waste and increasing productivity guarantees that our customers will receive top-notch products on schedule and within their allocated budget.
Overcoming Barriers: Tips for EMS Companies
- Start Small
Focus on a single production line or process to implement lean principles and gradually expand to other areas. - Invest in Training
Teach your employees about the benefits and practices of lean manufacturing in EMS. When you provide the right knowledge and tools, it empowers your team to identify and fix inefficiencies. - Leverage Technology
Utilize advanced tools like automation, IoT, and AI to enhance lean practices and maintain precision in production. - Collaborate with Partners
Work closely with suppliers and customers to align on lean goals and ensure seamless integration of processes.
Conclusion
The benefits of lean manufacturing in EMS extend far beyond cost savings. By using lean manufacturing techniques, companies can improve how fast they work, the quality of their products, and the time it takes to deliver them, making sure customers get great value quickly.
Moreover, the lean manufacturing process fosters innovation, sustainability, and employee engagement, all of which contribute to long-term success.
For EMS providers looking to improve performance and competitiveness, lean manufacturing offers a proven path forward. With its focus on continuous improvement and waste reduction, lean practices ensure that businesses stay agile, efficient, and ready to meet the demands of the future.